Method for preparing silicon tetrafluoride from calcium fluosilicate
A technology of silicon tetrafluoride and calcium fluorosilicate, which is applied in the direction of silicon halide compounds, halosilanes, etc., can solve the problems of difficult removal of silicon tetrafluoride, low yield of silicon tetrafluoride, and high cost of silicon tetrafluoride , to achieve the effects of improving energy utilization efficiency, light equipment corrosion, and reducing production costs
- Summary
- Abstract
- Description
- Claims
- Application Information
AI Technical Summary
Problems solved by technology
Method used
Image
Examples
Embodiment 1
[0020] A kind of preparation method of silicon tetrafluoride of the present invention, take calcium fluorosilicate hydrate as raw material, comprise the following steps:
[0021] (1) Dehydration: preheat the hydrated calcium fluorosilicate and send it into the dehydration reactor, and dry it for 150 minutes under the conditions of pressure 0.05 MPaG and temperature 100 ℃ to obtain a solid powder with a moisture content of 1.5wt%. Calcium hexafluorosilicate, the calcium hexafluorosilicate is discharged from the bottom of the dehydration reactor, and the water vapor and a small amount of solid particles generated by decomposition are discharged from the top of the dehydration reactor, and condensed water is obtained after being dedusted by a cyclone dust collector;
[0022] (2) Pyrolysis: send the calcium hexafluorosilicate obtained in step (1) into the intermediate storage tank, fill the intermediate storage tank with silicon tetrafluoride gas to remove the air and a small amoun...
Embodiment 2
[0025] A kind of preparation method of silicon tetrafluoride of the present invention, take calcium fluorosilicate hydrate as raw material, comprise the following steps:
[0026] (1) Dehydration: Preheat the hydrated calcium fluorosilicate to 60°C and send it into the dehydration reactor, and dry it for 90 minutes under the conditions of pressure of 0.2 MPaG and temperature of 170°C to obtain a solid with a moisture content of 1.5wt%. Powdered calcium hexafluorosilicate, the calcium hexafluorosilicate is discharged from the bottom of the dehydration reactor, and the water vapor and a small amount of solid particles generated by decomposition are discharged from the top of the dehydration reactor, and condensed water is obtained after being dedusted by a cyclone dust collector;
[0027] (2) Pyrolysis: send the calcium hexafluorosilicate obtained in step (1) into the intermediate storage tank, fill the intermediate storage tank with silicon tetrafluoride gas to remove the air and...
Embodiment 3
[0030] A method for preparing silicon tetrafluoride of the present invention, using calcium fluorosilicate hydrate as a raw material, comprises the following steps (as shown in Figure 3):
[0031] (1) Dehydration: The hydrated calcium fluorosilicate is preheated to 100°C by a calcium fluoride cooler, and then sent to the dehydration reactor, and dried for 60 minutes under the conditions of a pressure of 0.5MPaG and a temperature of 220°C to obtain the moisture content It is 1.5wt% solid powdery calcium hexafluorosilicate, and the calcium hexafluorosilicate is discharged from the bottom of the dehydration reactor, and the water vapor and a small amount of solid particles generated by decomposition are discharged from the top of the dehydration reactor;
[0032] (2) Pyrolysis: send the calcium hexafluorosilicate obtained in step (1) into the intermediate storage tank, fill the intermediate storage tank with silicon tetrafluoride gas to remove the air and a small amount of water v...
PUM
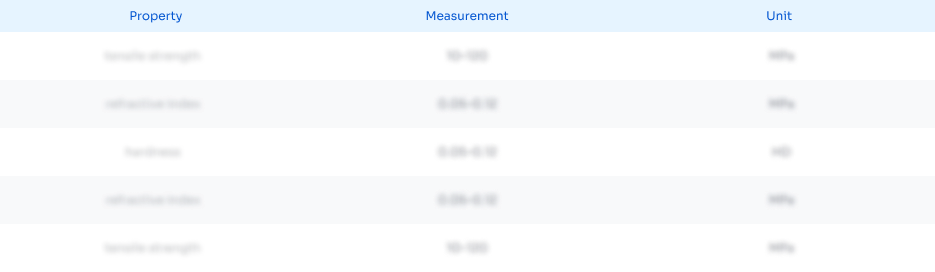
Abstract
Description
Claims
Application Information

- R&D
- Intellectual Property
- Life Sciences
- Materials
- Tech Scout
- Unparalleled Data Quality
- Higher Quality Content
- 60% Fewer Hallucinations
Browse by: Latest US Patents, China's latest patents, Technical Efficacy Thesaurus, Application Domain, Technology Topic, Popular Technical Reports.
© 2025 PatSnap. All rights reserved.Legal|Privacy policy|Modern Slavery Act Transparency Statement|Sitemap|About US| Contact US: help@patsnap.com