Method for recovering rhodium from inactivated rhodium-phosphine complex catalyst
A catalyst and complexation technology, applied in the field of rhodium recovery, can solve problems such as complex recovery process and pollution, and achieve the effects of simplified process flow, simple equipment and low pollution
- Summary
- Abstract
- Description
- Claims
- Application Information
AI Technical Summary
Problems solved by technology
Method used
Examples
Embodiment 1
[0031] The used catalyst waste liquid is an inactivated catalyst in the process of producing butyraldehyde through the hydroformylation reaction of propylene, carbon monoxide and hydrogen, and its activity is reduced to below 30% of that of the fresh catalyst.
[0032]The catalyst waste liquid was concentrated on a scraped thin film evaporation device. The concentration of rhodium in the resulting concentrated waste liquid is 1700ppm, containing 6.5wt% of triphenylphosphine, 11.1% of triphenylphosphine oxide, and the rest are butyraldehyde trimers and polymers, high-boiling point organic by-products, and other small amounts of metals Impurities.
[0033] Weigh 24.97 g of the above-mentioned concentrated catalyst waste liquid and add it into a 500 ml three-neck flask, then add 200 ml of absolute ethanol, and stir to make it evenly mixed. Air is introduced into the mixed solution in the flask, and the air is bubbled through the bottom of the liquid through an immersion tube, so...
Embodiment 2
[0035] Weigh 26.79 g of the concentrated catalyst waste liquid in Example 1 and add it into a 500 ml three-neck flask, then add 200 ml of absolute ethanol, and stir to make it evenly mixed. Air is introduced into the liquid in the flask, and the air is bubbled through the bottom of the liquid through an immersion tube, so that the oxygen and the catalyst waste liquid are fully contacted and reacted, and the flow rate of the air is 100ml / min. Stir and slowly raise the temperature to 90°C, stop feeding air after 24 hours of reaction. During this process triphenylphosphine has been substantially completely oxidized to triphenylphosphine oxide. Then the temperature of the reaction system was lowered to 70° C., 50 ml of 20% NaOH ethanol solution was added to the flask, and the reaction was continued at 70° C. for 5 h, and then cooled to room temperature. Filter, remove the solvent, wash with distilled water and ethanol respectively, and dry under vacuum at 50°C to obtain 0.31 g of...
Embodiment 3
[0037] Weigh 25.54 g of the concentrated catalyst waste liquid in Example 1 and add it into a 500 ml three-necked flask, then add 100 ml of absolute ethanol, and stir to make it evenly mixed. Add 2ml of tert-butyl hydroperoxide to the flask, slowly heat to 60°C, and react for 15h. Then add 5.06g of NaOH powder, heat to 70°C, continue the reaction for 3h, then cool down to room temperature. Filter, remove the solvent, wash with distilled water and ethanol respectively, and dry under vacuum at 50°C to obtain 0.28 g of a yellow-brown solid. Elemental analysis showed that the yield was 65% based on rhodium atoms.
PUM
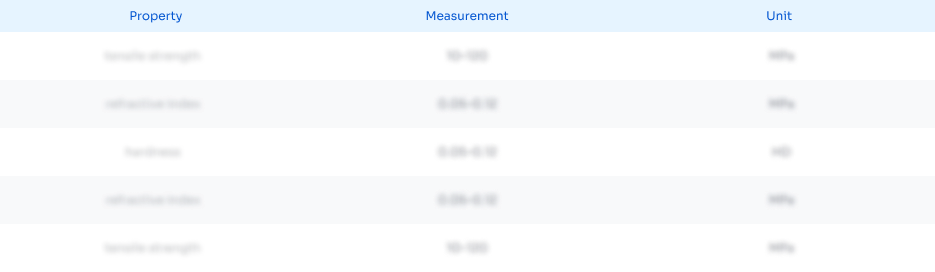
Abstract
Description
Claims
Application Information

- R&D Engineer
- R&D Manager
- IP Professional
- Industry Leading Data Capabilities
- Powerful AI technology
- Patent DNA Extraction
Browse by: Latest US Patents, China's latest patents, Technical Efficacy Thesaurus, Application Domain, Technology Topic, Popular Technical Reports.
© 2024 PatSnap. All rights reserved.Legal|Privacy policy|Modern Slavery Act Transparency Statement|Sitemap|About US| Contact US: help@patsnap.com