Method for recovering ferrocene derivatives and ammonium perchlorate from composite solid propellant
A technology of ferrocene derivatives and solid propellants, applied in the direction of perchloric acid, perchlorate, chemical instruments and methods, etc., can solve the problems of poor safety, complicated process, low recovery rate, etc., and achieve high recovery rate , good quality and cheap price
- Summary
- Abstract
- Description
- Claims
- Application Information
AI Technical Summary
Problems solved by technology
Method used
Examples
Embodiment 1
[0020] Soaking step: soak the composite solid propellant to be treated with dichloromethane, the soaking temperature is 10°C, and the soaking time is 48h;
[0021] Distillation step: take out the composite solid propellant in the dichloromethane, distill the dichloromethane to obtain crude ferrocene derivatives; the ferrocene derivatives are mainly tert-butyl ferrocene and cattosine;
[0022] Purification step: Purify the crude ferrocene derivative by recrystallization method, the solvent used in the recrystallization method is pentane, and the recovery rate reaches 99.3%;
[0023] Extraction step: extract the soaked composite solid propellant in a saturated solution of ammonium perchlorate, the extraction temperature is 40°C, and the extraction time is 24 hours;
[0024] Recrystallization step: take out the composite solid propellant in the extractant, cool the extractant to 0°C to form a supersaturated solution of ammonium perchlorate, recrystallize ammonium perchlorate crys...
Embodiment 2
[0026] Soaking step: soak the composite solid propellant to be treated with 1,2-dichloroethane, the soaking temperature is 80°C, and the soaking time is 1h;
[0027] Distillation step: take out the composite solid propellant in 1,2-dichloroethane, distill 1,2-dichloroethane to obtain crude ferrocene derivatives; ferrocene derivatives are mainly tert-butyl di Ferrocene, Catoxin;
[0028] Purification step: Purify the crude ferrocene derivative by recrystallization method, the solvent used in the recrystallization method is cyclohexane, and the recovery rate reaches 99.3%;
[0029] Extraction step: extract the soaked composite solid propellant in a saturated solution of ammonium perchlorate, the extraction temperature is 90°C, and the extraction time is 3 hours;
[0030] Recrystallization step: take out the composite solid propellant in the extractant, cool the extractant to 0°C to form a supersaturated solution of ammonium perchlorate, recrystallize ammonium perchlorate crysta...
Embodiment 3
[0033] Soaking step: Soak the composite solid propellant to be treated with N,N-dimethylacetamide, the soaking temperature is 60°C, and the soaking time is 8h;
[0034] Distillation step: take out the composite solid propellant in N,N-dimethylacetamide, distill N,N-dimethylacetamide to obtain crude ferrocene derivatives; ferrocene derivatives are mainly tert-butyl Base ferrocene, catocine;
[0035] Purification steps: Purify the crude ferrocene derivatives by sublimation method, and the recovery rate reaches 99.3%;
[0036] Extraction step: extract the soaked composite solid propellant in a saturated solution of ammonium perchlorate, the extraction temperature is 80°C, and the extraction time is 12 hours;
[0037] Recrystallization step: take out the composite solid propellant in the extractant, cool the extractant to 40°C to form a supersaturated solution of ammonium perchlorate, recrystallize ammonium perchlorate crystals, and the recovery rate reaches 99.5%.
PUM
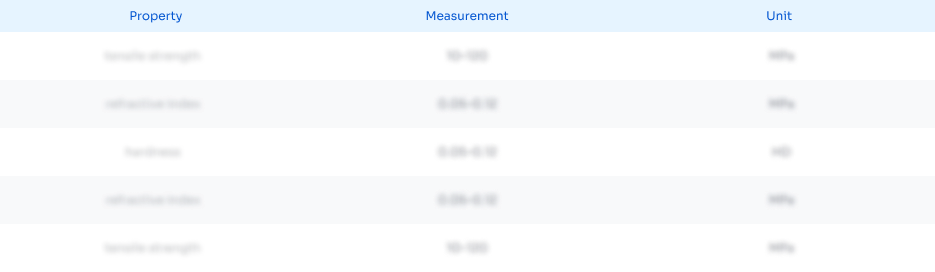
Abstract
Description
Claims
Application Information

- R&D Engineer
- R&D Manager
- IP Professional
- Industry Leading Data Capabilities
- Powerful AI technology
- Patent DNA Extraction
Browse by: Latest US Patents, China's latest patents, Technical Efficacy Thesaurus, Application Domain, Technology Topic, Popular Technical Reports.
© 2024 PatSnap. All rights reserved.Legal|Privacy policy|Modern Slavery Act Transparency Statement|Sitemap|About US| Contact US: help@patsnap.com