Vacuum semi-continuous method for casting copper chromium zirconium alloy
A copper-chromium-zirconium, semi-continuous technology, which is applied in the field of non-vacuum semi-continuous melting and casting of copper-chromium-zirconium alloys, can solve the problems of large air intake of high-temperature melts, prone to oxidation reactions, and difficult to effectively add, etc., to achieve alloy composition control The effects of stability, chemical composition up to standard, and production capacity improvement
- Summary
- Abstract
- Description
- Claims
- Application Information
AI Technical Summary
Problems solved by technology
Method used
Image
Examples
Embodiment 1
[0024] Embodiment 1: A kind of method for non-vacuum semi-continuous melting and casting of copper-chromium-zirconium alloy adopts the following process steps:
[0025] (1) 58% copper and 38% zirconium are smelted in a vacuum furnace by mass percentage to obtain a copper-zirconium master alloy for subsequent use; the vacuum in the vacuum furnace is 10Pa, the smelting temperature is 1400°C, and the smelting time is 70 minutes; commercially available copper-zirconium master alloys can also be used;
[0026] (2) According to the composition and proportioning ratio of copper-chromium-zirconium alloy, the unit is mass percentage: copper-zirconium master alloy with zirconium equivalent of 0.1%, metal chromium 1.2%, and the balance is cathode copper;
[0027] (3) Put the cathode copper into the intermediate frequency furnace for smelting, the smelting temperature is 1250°C, and the smelting time is 70 minutes; add deoxidizer pure magnesium for degassing and deoxidation, the amount of...
Embodiment 2
[0032] Embodiment two: a kind of method for non-vacuum semi-continuous melting and casting copper-chromium-zirconium alloy adopts the following process steps:
[0033] (1) 62% copper and 42% zirconium are smelted in a vacuum furnace by mass percentage to obtain a copper-zirconium master alloy for subsequent use; the vacuum degree in the vacuum furnace is 15Pa, the melting temperature is 1500° C., and the melting time is 60 minute;
[0034] (2) According to the composition and proportioning ratio of copper-chromium-zirconium alloy, the unit is mass percentage: copper-zirconium master alloy with zirconium equivalent of 0.11%, metal chromium 1.18%, and the balance is cathode copper;
[0035] (3) Put the cathode copper into the intermediate frequency furnace for smelting, the smelting temperature is 1300°C, and the smelting time is 60 minutes; add deoxidizer pure magnesium for degassing and deoxidation, the amount of pure magnesium added is 0.06% of the weight of the copper-chromi...
Embodiment 3
[0040] Embodiment three: a kind of method for non-vacuum semi-continuous melting and casting copper chromium zirconium alloy, adopt following process step:
[0041] (1) 59% copper and 39% zirconium are smelted in a vacuum furnace by mass percentage to obtain a copper-zirconium master alloy for subsequent use; the vacuum degree in the vacuum furnace is 11Pa, the smelting temperature is 1420° C., and the smelting time is 62 minute;
[0042] (2) According to the composition and proportioning ratio of copper-chromium-zirconium alloy, the unit is mass percentage: copper-zirconium master alloy with zirconium equivalent of 0.12%, metal chromium 1.14%, and the balance is cathode copper;
[0043] (3) Put the cathode copper into the intermediate frequency furnace for smelting, the smelting temperature is 1260°C, and the smelting time is 62 minutes; add deoxidizer pure magnesium for degassing and deoxidation, the amount of pure magnesium added is 0.045% of the weight of the copper-chromi...
PUM
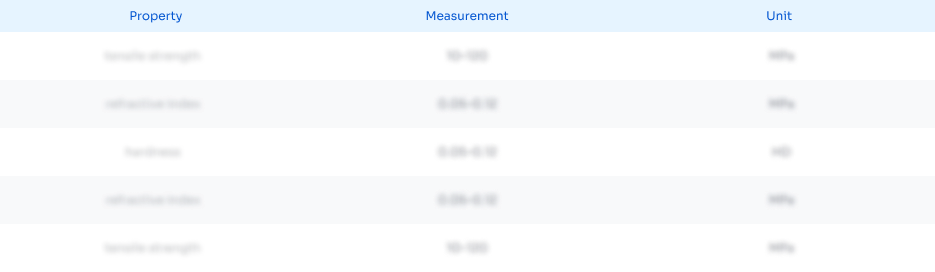
Abstract
Description
Claims
Application Information

- R&D Engineer
- R&D Manager
- IP Professional
- Industry Leading Data Capabilities
- Powerful AI technology
- Patent DNA Extraction
Browse by: Latest US Patents, China's latest patents, Technical Efficacy Thesaurus, Application Domain, Technology Topic, Popular Technical Reports.
© 2024 PatSnap. All rights reserved.Legal|Privacy policy|Modern Slavery Act Transparency Statement|Sitemap|About US| Contact US: help@patsnap.com