Dry-type permanent magnetic roller for separation of fine-disseminated ore
A mineral sorting and magnetic roller technology, which is applied in the fields of magnetic separation, solid separation, chemical instruments and methods, etc., can solve problems such as affecting product quality and recovery rate, problems with magnet fixing methods, and ineffective use of magnetic fields.
- Summary
- Abstract
- Description
- Claims
- Application Information
AI Technical Summary
Problems solved by technology
Method used
Image
Examples
Embodiment Construction
[0020] The present invention will be further described below in conjunction with embodiment (accompanying drawing):
[0021] Such as figure 1 , 2 As shown, the dry-type permanent magnetic roller for the separation of fine-grained embedded minerals of the present invention is characterized in that: the magnetic roller includes a mandrel 1, which is sleeved on the mandrel in a manner coaxial with the mandrel 1 1, the non-magnetic cylinder 9 on the non-magnetic cylinder 9 is successively set with stainless steel rings 5 and low-carbon steel rings 6; the outer ring surface of each low-carbon steel ring 6 is equipped with Several fan-shaped magnets 4 arranged at intervals, in the axial direction, between two adjacent fan-shaped magnets 4 are separated by a magnetic steel spacer ring 7 and a magnetic steel spacer ring rib 8, and the magnetic steel spacer ring 7 and the magnetic steel spacer rib 8 are non-magnetic materials, and welded together (see Figure 5 , 6 , 7, 8), this ...
PUM
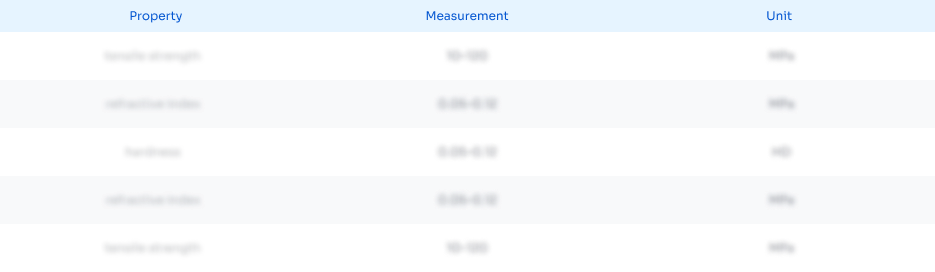
Abstract
Description
Claims
Application Information

- R&D
- Intellectual Property
- Life Sciences
- Materials
- Tech Scout
- Unparalleled Data Quality
- Higher Quality Content
- 60% Fewer Hallucinations
Browse by: Latest US Patents, China's latest patents, Technical Efficacy Thesaurus, Application Domain, Technology Topic, Popular Technical Reports.
© 2025 PatSnap. All rights reserved.Legal|Privacy policy|Modern Slavery Act Transparency Statement|Sitemap|About US| Contact US: help@patsnap.com