Method for processing catalytic converter for automobile
A processing method and catalyst technology, which are applied in the field of automobile post-treatment emission systems, can solve the problems of increasing gasket failure, carrier crushing, increasing manufacturing cost, etc., so as to reduce welding processes and necking processes, improve mechanical durability, reduce effect of cost increase
- Summary
- Abstract
- Description
- Claims
- Application Information
AI Technical Summary
Problems solved by technology
Method used
Image
Examples
Embodiment Construction
[0027] A method for processing a catalytic converter for automobiles, comprising:
[0028] 1) Roll the cylinder plate into the shape of the outer shell of the catalytic converter and round it;
[0029] 2) Fix the rolled cylinder body 1 by straight seam welding;
[0030] 3) Cut the two ends of the welded cylinder to the specified length, and remove the defective welds at the two ends;
[0031] 4) Wrap the liner 2 on the carrier 3 with adhesive tape, pay attention to the offset of the liner when it is pressed in;
[0032] 5) Press the wrapped carrier 3 into the barrel 1;
[0033] 6) Put the cylinder body 1 into the spinning jig for spinning;
[0034] 7) The thrust displacement test is carried out on the catalytic converter assembly after spinning.
[0035] Wherein, the spinning in step 6) is to spin out the end cone 5 structure at both ends of the barrel 1 .
[0036] The schematic diagram of the structure of the catalytic converter processed by the above processing method i...
PUM
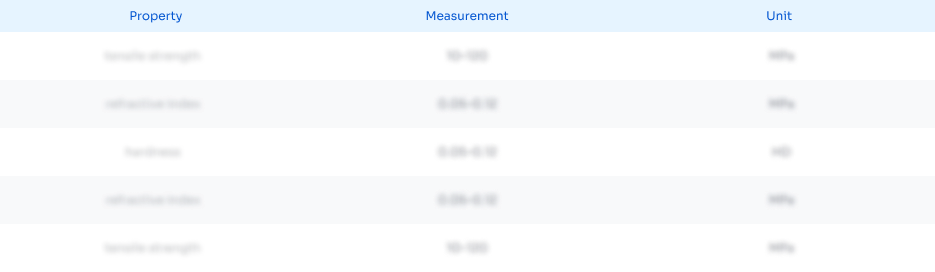
Abstract
Description
Claims
Application Information

- R&D Engineer
- R&D Manager
- IP Professional
- Industry Leading Data Capabilities
- Powerful AI technology
- Patent DNA Extraction
Browse by: Latest US Patents, China's latest patents, Technical Efficacy Thesaurus, Application Domain, Technology Topic, Popular Technical Reports.
© 2024 PatSnap. All rights reserved.Legal|Privacy policy|Modern Slavery Act Transparency Statement|Sitemap|About US| Contact US: help@patsnap.com