Optical fiber end surface processing method
An optical fiber end face treatment and optical fiber end face technology, which is applied to the coupling of optical waveguides and other directions, can solve the problems of complex production process of the optical fiber grinding treatment method, poor optical fiber loss and reflection loss indicators, high manufacturing cost and difficulty, and avoid adverse effects. , Guaranteed physical contact, low cost effect
- Summary
- Abstract
- Description
- Claims
- Application Information
AI Technical Summary
Problems solved by technology
Method used
Image
Examples
Embodiment Construction
[0016] In conjunction with the accompanying drawings, the present invention is described in detail.
[0017] Such as figure 1 As shown, to prepare the fiber end face, the fiber end 1 is cleaved into a smooth fiber end face a by the fiber cleaver, and the fiber end face a has a certain inclination angle affected by the precision of the cleaver.
[0018] Such as figure 2 As shown, the cut optical fiber end 1 is positioned in the heat source A, and the heat source A and the intensity of the heat source A can be properly adjusted according to the different optical fiber materials and the application of the optical fiber.
[0019] Such as image 3 Shown: using electric arc, laser or flame and other thermal melting treatment methods, the completely cut optical fiber end 1 is finitely melted, and the limitedly fused optical fiber end 1 is formed into a smooth spherical or quasi-spherical surface b by the surface tension of the liquid, and after cooling and solidification Complet...
PUM
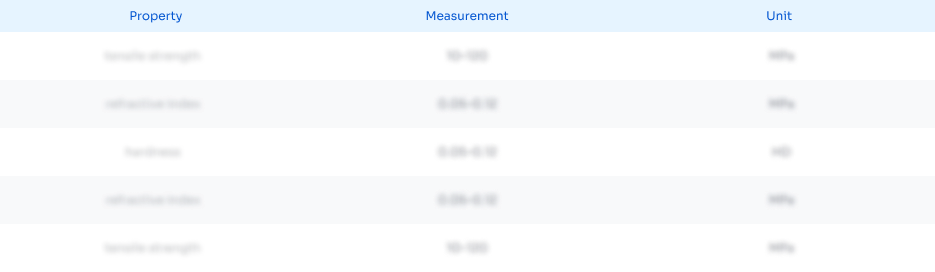
Abstract
Description
Claims
Application Information

- R&D
- Intellectual Property
- Life Sciences
- Materials
- Tech Scout
- Unparalleled Data Quality
- Higher Quality Content
- 60% Fewer Hallucinations
Browse by: Latest US Patents, China's latest patents, Technical Efficacy Thesaurus, Application Domain, Technology Topic, Popular Technical Reports.
© 2025 PatSnap. All rights reserved.Legal|Privacy policy|Modern Slavery Act Transparency Statement|Sitemap|About US| Contact US: help@patsnap.com