Preparation method for flame-retardant spinning viscose
A technology for spinning viscose and viscose, which is applied in the field of preparation of flame retardant spun viscose, can solve the problems of uneven mixing of flame retardants in the flame retardant viscose, poor spinnability, and difficulty in operation, etc. Stable spinnability, guaranteed dispersion uniformity, easy operation
- Summary
- Abstract
- Description
- Claims
- Application Information
AI Technical Summary
Problems solved by technology
Method used
Examples
Embodiment 1
[0017] Add sodium metasilicate pentahydrate into the dissolved viscose solution, and stir evenly to prepare a flame retardant solution with an effective flame retardant concentration of 4.5 wt%.
[0018] Using cotton pulp as raw material, the cellulose xanthate viscose is prepared through steps including dipping, pressing, crushing, aging and yellowing.
[0019] Add the prepared flame retardant solution into the cellulose xanthate viscose, mix and stir to dissolve, and filter, mature, and defoam to obtain a cellulose content of 9.06wt%. The effective content of sodium hydroxide is 30.8wt%, the sodium hydroxide content is 7.23wt%, the viscosity measured by the falling ball method is 32s, and 10%NH 4 The degree of maturity measured by Cl is 25ml flame retardant spun viscose.
Embodiment 2
[0021] Add anhydrous sodium metasilicate to the dissolved viscose solution, and stir evenly to prepare a flame retardant solution with an effective flame retardant concentration of 4.8 wt%.
[0022] Using wood pulp as raw material, the cellulose xanthate viscose is prepared through steps including dipping, pressing, crushing, aging and yellowing.
[0023] Add the prepared flame retardant solution into the cellulose xanthate viscose, mix and stir to dissolve, and filter, ripen, and defoam to obtain a cellulose content of 9.8wt%. The effective content of sodium hydroxide is 31.2wt%, the sodium hydroxide content is 7.84wt%, the viscosity measured by the falling ball method is 35s, and 10%NH 4 The degree of ripeness measured by Cl is 22ml of flame-retardant spun viscose.
Embodiment 3
[0025] Add anhydrous sodium metasilicate to the dissolved viscose solution, and stir evenly to prepare a flame retardant solution with an effective flame retardant concentration of 8.2 wt%.
[0026] Using cotton pulp as raw material, the cellulose xanthate viscose is prepared through steps including dipping, pressing, crushing, aging and yellowing.
[0027] Add the prepared flame retardant solution into the cellulose xanthate viscose, mix and stir to dissolve, and filter, ripen, and defoam to obtain a cellulose content of 10.06wt%. The effective content of sodium hydroxide is 34.5wt%, the sodium hydroxide content is 8.04wt%, the viscosity measured by the falling ball method is 36s, and 10%NH 4 Flame-retardant spun viscose with a maturity of 20ml measured by Cl.
PUM
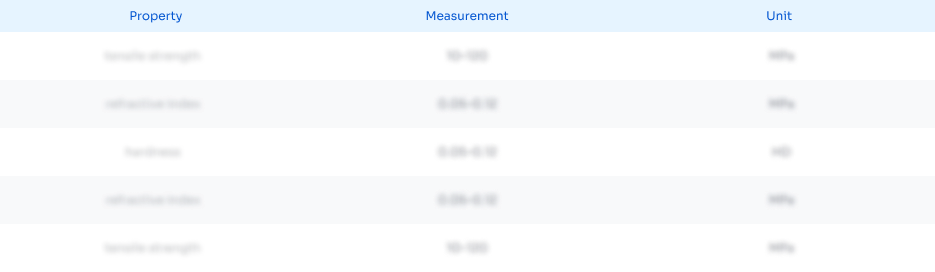
Abstract
Description
Claims
Application Information

- R&D
- Intellectual Property
- Life Sciences
- Materials
- Tech Scout
- Unparalleled Data Quality
- Higher Quality Content
- 60% Fewer Hallucinations
Browse by: Latest US Patents, China's latest patents, Technical Efficacy Thesaurus, Application Domain, Technology Topic, Popular Technical Reports.
© 2025 PatSnap. All rights reserved.Legal|Privacy policy|Modern Slavery Act Transparency Statement|Sitemap|About US| Contact US: help@patsnap.com