Highly-toughened bulk molding composition
A bulk molding compound and toughening technology, applied in the field of high toughening bulk molding compound, can solve the problems of decreased tensile strength and no significant improvement, and achieve the effect of improving toughness
- Summary
- Abstract
- Description
- Claims
- Application Information
AI Technical Summary
Problems solved by technology
Method used
Examples
Embodiment 1
[0022] A highly toughened bulk molding compound (BMC), which is obtained by polymerization of the following raw materials in parts by weight, wherein:
[0023] Resin 65
[0024] PSt 30
[0025] TBPB 1.0
[0026] TBPO0.5
[0028] Vinyl terminated liquid nitrile rubber 8
[0029] Calcium Carbonate Whiskers 40
[0030] Styrylaminofunctional Silane 2.5
[0032] 6mm glass fiber 70
[0033] The polymerization reaction is as follows: add the weighed m-phenylene resin, PMMA, TBPB, TBPO, zinc stearate, vinyl-terminated liquid nitrile rubber, calcium carbonate whiskers, and styryl amino functional group silane into the high-speed disperser and stir Dispersion, the speed of the high-speed mixer is 1200 rpm, and the stirring and dispersing time is 7 minutes from the addition of the material to the end; the calcium agglomerate is introduced into the BMC kneader, and then the dispersed resin paste is poured into the BMC kne...
Embodiment 2
[0036] Another highly toughened bulk molding compound (BMC), which is obtained by polymerization of the following raw materials in parts by weight, wherein:
[0037] Resin 65
[0038] PSt 30
[0039] TBPB 1.0
[0040] TBPO0.5
[0042] Vinyl terminated liquid nitrile rubber 14
[0043] Calcium Carbonate Whiskers 40
[0044] Styrylaminofunctional Silane 2.5
[0045] Calcium carbonate 200
[0046] 6mm glass fiber 70
[0047] The polymerization reaction is as follows: add the weighed m-phenylene resin, PMMA, TBPB, TBPO, zinc stearate, vinyl-terminated liquid nitrile rubber, calcium carbonate whiskers, and styryl amino functional group silane into the high-speed disperser and stir Dispersion, the speed of the high-speed mixer is 1200 rpm, and the stirring and dispersing time is 7 minutes from the addition of the material to the end; the calcium agglomerate is introduced into the BMC kneader, and then the dispersed resin paste is poured into the ...
PUM
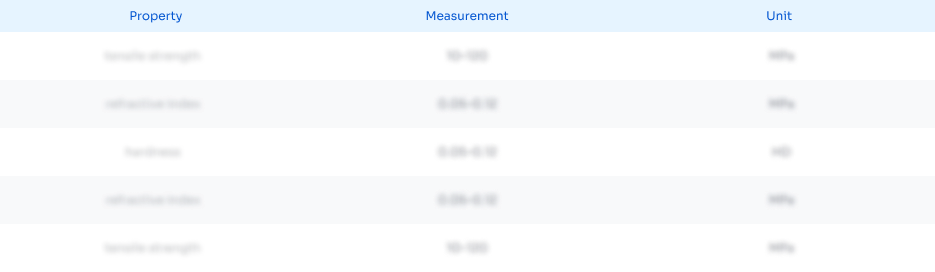
Abstract
Description
Claims
Application Information

- Generate Ideas
- Intellectual Property
- Life Sciences
- Materials
- Tech Scout
- Unparalleled Data Quality
- Higher Quality Content
- 60% Fewer Hallucinations
Browse by: Latest US Patents, China's latest patents, Technical Efficacy Thesaurus, Application Domain, Technology Topic, Popular Technical Reports.
© 2025 PatSnap. All rights reserved.Legal|Privacy policy|Modern Slavery Act Transparency Statement|Sitemap|About US| Contact US: help@patsnap.com