Fully plastic wood-imitation material and preparation method thereof
A technology of imitation wood material and inorganic filling material, applied in the field of imitation wood material and its preparation, can solve the problems of few reports on the preparation technology of imitation wood material, the waterproof performance needs to be improved, the products are easy to absorb moisture, etc. Convenient construction, natural and realistic texture
- Summary
- Abstract
- Description
- Claims
- Application Information
AI Technical Summary
Problems solved by technology
Method used
Image
Examples
Embodiment 1
[0020] Mix nano-SiCl, 1 nano-calcium carbonate, and 10 parts of ABS resin, and dry at 80°C for 2 hours in a drier. At the same time, 0.2 parts of UV-531 (ultraviolet absorber), polyethylene wax / lithium complex soap 1:1) 0.2 parts, sandalwood wood oil 0.4 parts, polybutylacrylate PBACOOH 0.7 parts, zinc oxide / iron oxide red / carbon black (2:2:1) 0.5 parts, mix well, and then mix the above two groups of mixtures with PS100 parts , 25 parts of HIPS are mixed, the final mixture is extruded and granulated in a twin-screw extruder, and finally the obtained granules are extruded and processed in the extruder.
[0021] The product was tested for tensile strength, bending strength, water absorption, heat shrinkage, etc. The results are shown in Table 1 and Table 2.
Embodiment 2
[0023] Nano BaSO 4 2 parts, 2 parts of nano-calcium carbonate, 13 parts of AS / PMMA resin (8:5) were mixed, and dried in a dryer at 80°C for two hours. At the same time, 0.3 parts of UV-531 (ultraviolet absorber), 0.6 parts of calcium stearate / zinc stearate / amino silicone oil (1:1:1), 0.3 parts of cloud wood oil, and 0.7 parts of polybutylacrylate PBACOOH , 1 part of benzidine yellow / quinacridone purple (3:2) is mixed, then the above two groups of mixtures are mixed with 100 parts of PS and 30 parts of HIPS, and the final mixture is extruded and granulated in a twin-screw extruder, and finally the The resulting pellets are injection molded by injection molding equipment.
[0024] The product was tested for tensile strength, bending strength, water absorption, heat shrinkage and other properties, and the results are shown in Tables 1 and 2.
Embodiment 3
[0026] nano-SiO 2 3 parts, 3 parts of nano-calcium carbonate, 15 parts of ABS / AS / PMMA resin (6:6:3), mixed in a dryer at 80°C for two hours. At the same time, 0.5 part of UV-531 (ultraviolet absorber), 0.7 part of polyethylene wax / amino silicone oil (3:4), 0.5 part of camphor wood essential oil, 1 part of polybutyl acrylate PBACOOH, benzidine yellow and quinacridone purple 1.5 parts of Everlasting Yellow HR (2:2:1) were mixed, and then the above two groups of mixtures were mixed with 100 parts of PS and 35 parts of HIPS, and the final mixture was extruded and granulated in a twin-screw extruder, and finally the obtained granules The material is extruded and processed in an extruder, or injection molded by injection molding equipment.
[0027] The product was tested for tensile strength, bending strength, water absorption, heat shrinkage and other properties, and the results are shown in Tables 1 and 2.
PUM
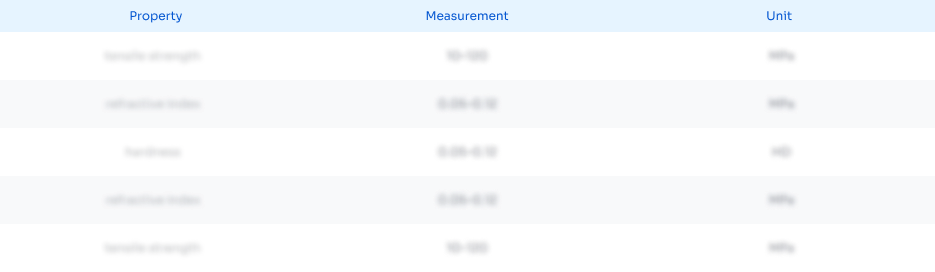
Abstract
Description
Claims
Application Information

- R&D
- Intellectual Property
- Life Sciences
- Materials
- Tech Scout
- Unparalleled Data Quality
- Higher Quality Content
- 60% Fewer Hallucinations
Browse by: Latest US Patents, China's latest patents, Technical Efficacy Thesaurus, Application Domain, Technology Topic, Popular Technical Reports.
© 2025 PatSnap. All rights reserved.Legal|Privacy policy|Modern Slavery Act Transparency Statement|Sitemap|About US| Contact US: help@patsnap.com