Method for preparing cerealose or maltose syrup with crushed rice enzyme method
A technology of maltose syrup and crushed material, which is applied in the field of maltose or maltose syrup preparation, which can solve the problems of high gelatinization temperature, difficult liquefaction, and difficulty in heat gelatinization, etc.
- Summary
- Abstract
- Description
- Claims
- Application Information
AI Technical Summary
Problems solved by technology
Method used
Examples
Embodiment 1
[0039] (1) Washing and other treatments: 100 parts by weight (dry weight) of rice crushed material is dusted and iron-removed, then transported to the pulverizer, crushed through 20 meshes, and then transported to the rice washing tank, and put water into the rice washing tank to soak the rice. crushed material, and then enter the compressed air to make the rice crushed material tumble and rub against each other in the water, rinse off the fine dust and other impurities adsorbed on the surface of the rice crushed material, the impurities float out from the overflow port, and release the rice washing water after rinsing. So repeated washing 2 times, the material is washed;
[0040] (2) Refining and pulping: put the washed rice crushed material into water and soak for 60 minutes, and the soaked rice crushed material is refined with a grinding wheel mill with a wet grinding method to obtain a slurry, pass through a 60-mesh sieve, and dry the slurry The substance mass concentratio...
Embodiment 2
[0045] (1) Cleaning and other treatments: 100 parts by weight (dry weight, the same below) of rice pulverized material is blown dust and iron removed and then transported to the pulverizer, crushed to 20 mesh and then transported to the rice washing tank, and put water into the rice washing tank for use Soak the rice crushed material in water, and then pass in compressed air to make the rice crushed material tumble and rub against each other in the water, rinse away the fine dust and other impurities adsorbed on the surface of the rice crushed material, and the impurities float out from the overflow port, and then release the washed rice after rinsing. Feed water, so repeated washing 2 times, the material is washed;
[0046] (2) Refining and pulping: put the washed rice crushed material into water and soak for 30 minutes, and the soaked rice crushed material is refined with a grinding wheel mill with a wet grinding method to obtain a slurry, pass through a 60-mesh sieve, and dr...
Embodiment 3
[0051] (1) Cleaning and other treatments: 100 parts by weight (dry weight, the same below) of rice pulverized material is blown dust and iron removed and then transported to the pulverizer, crushed to 20 mesh and then transported to the rice washing tank, and put water into the rice washing tank for use Soak the rice crushed material in water, and then pass in compressed air to make the rice crushed material tumble and rub against each other in the water, rinse away the fine dust and other impurities adsorbed on the surface of the rice crushed material, and the impurities float out from the overflow port, and then release the washed rice after rinsing. Feed water, wash again 1 time, wash the material;
[0052] (2) Refining and pulping: put the washed rice crushed material into water and soak for 60 minutes, and the soaked rice crushed material is refined with a grinding wheel mill with a wet grinding method to obtain a slurry, pass through a 60-mesh sieve, and dry the slurry T...
PUM
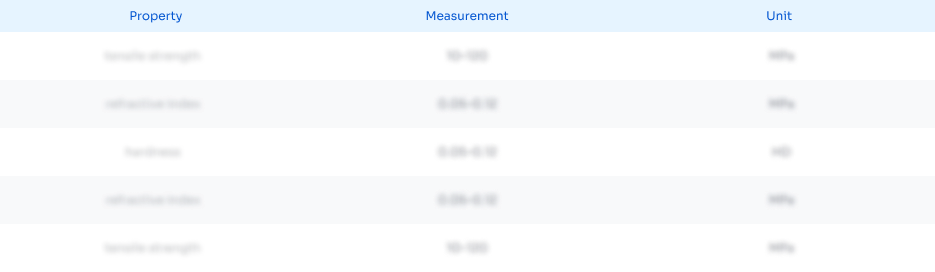
Abstract
Description
Claims
Application Information

- R&D
- Intellectual Property
- Life Sciences
- Materials
- Tech Scout
- Unparalleled Data Quality
- Higher Quality Content
- 60% Fewer Hallucinations
Browse by: Latest US Patents, China's latest patents, Technical Efficacy Thesaurus, Application Domain, Technology Topic, Popular Technical Reports.
© 2025 PatSnap. All rights reserved.Legal|Privacy policy|Modern Slavery Act Transparency Statement|Sitemap|About US| Contact US: help@patsnap.com