Vacuum plating method for PP (polypropylene) plastic and UV (ultraviolet) oil used therein
A vacuum electroplating and plastic technology, applied in the direction of polyester paint, coating, etc., can solve the problems of PP plastic deformation, plastic aging resistance, reduced durability, and failure to meet fire safety requirements, so as to improve aging resistance and durability , Saving procedures, improving efficiency and the effect of qualified product rate
- Summary
- Abstract
- Description
- Claims
- Application Information
AI Technical Summary
Problems solved by technology
Method used
Examples
Embodiment 1
[0028] Example 1. The percentage by weight of each component of the selected PP treatment agent is 90% toluene and 10% polyolefin with functional groups. The weight percent of each component of the base oil matched with the PP treatment agent is: toluene 15, ethyl acetate 20, xylene 5, polyester acrylate resin 25, pure acrylate resin 18, active monomer TMPTA 11, acrylates Leveling agent 0.1, phosphate adhesion aid 0.9, photoinitiator 5.
Embodiment 2
[0029] Example 2. The percentage by weight of each component of the selected PP treatment agent is 75% of toluene and 25% of polyolefin with functional groups. The percentage by weight of each component of the base oil matched with the PP treatment agent is, toluene 18, ethyl acetate 25, xylene 5, polyester acrylate resin 12, pure acrylate resin 12, active monomer TMPTA 18, acrylates Leveling agent 0.2, phosphate adhesion aid 1.8, photoinitiator 8.
Embodiment 3
[0030] Example 3. The percentage by weight of each component of the selected PP treatment agent is 82% toluene and 18% polyolefin with functional groups. The percentage by weight of each component of the base oil matched with the PP treatment agent is, toluene 16, ethyl acetate 28, xylene 9, polyester acrylate resin 12, pure acrylate resin 12, active monomer TMPTA 15, acrylates Leveling agent 0.2, phosphate adhesion aid 1.8, photoinitiator 6.
PUM
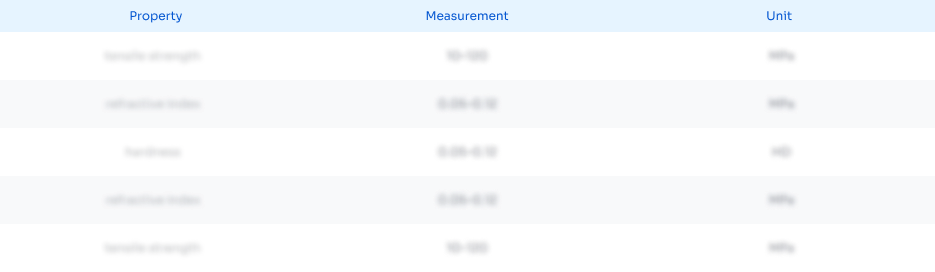
Abstract
Description
Claims
Application Information

- R&D
- Intellectual Property
- Life Sciences
- Materials
- Tech Scout
- Unparalleled Data Quality
- Higher Quality Content
- 60% Fewer Hallucinations
Browse by: Latest US Patents, China's latest patents, Technical Efficacy Thesaurus, Application Domain, Technology Topic, Popular Technical Reports.
© 2025 PatSnap. All rights reserved.Legal|Privacy policy|Modern Slavery Act Transparency Statement|Sitemap|About US| Contact US: help@patsnap.com