Automobile fuel in-tank tube and method of manufacturing same
A manufacturing method, fuel tank technology, applied in the direction of liquid fuel feeder, application, hose, etc., to achieve excellent resistance, inhibit decomposition reaction, and prevent clogging of injectors
- Summary
- Abstract
- Description
- Claims
- Application Information
AI Technical Summary
Problems solved by technology
Method used
Image
Examples
Embodiment 1
[0067] Aliphatic polyamide resin (I) that is polyamide 11 is extruded into a tube shape (inner diameter: 6mm, outer diameter: 8mm), and then vacuum forming corrugator (vacuum forming corrugator) (manufactured by Japan "Korma" Co., Ltd. , model 120HS) to form a corrugated structure (corrugated structure part: 150mm, outer diameter of valley / peak outer diameter = 7mm / 10mm, pitch length: 3mm) (straight parts at both ends: 10mm, inner diameter of straight parts at both ends: 6mm, Outer diameter: 8mm). Next, it is irradiated with an electron beam (a dose of 250 kGy), and cut into a predetermined length (180 mm in length) by a cutter or the like. Next, put the cut tube into a heat treatment furnace (made by Japan "Espec" company, PV(H)-212), and heat-treat it (150°C x 30 minutes), thereby producing a box-in-box tube (with the above-mentioned inner diameter, outer diameter ).
Embodiment 2~6
[0068] (Examples 2-6, Comparative Examples 1-4)
[0069] Inner tubes were produced as in Example 1 except that the type of aliphatic polyamide resin, the conditions of electron beam irradiation and heat treatment, etc. were changed as shown in Tables 1 and 2 below.
[0070] Table 1
[0071]
[0072] Table 2
[0073]
[0074] Using the tank tubes of Examples and Comparative Examples obtained in this way, each property was evaluated according to the following criteria. These results are shown together in Table 1 and Table 2 above.
[0075] (breaking pressure)
[0076] (initial room temperature (23°C))
[0077] Fill the tube in the box with silicone oil as a pressurized medium, use the test pipe to plug both ends of the tube in the box, and conduct a pressure test at room temperature (23°C) at a pressure increase rate of 1.0MPa / min to measure the rupture of the tube in the box Or the pressure when the test pipe is disconnected (destroying pressure).
[0078] In the ev...
PUM
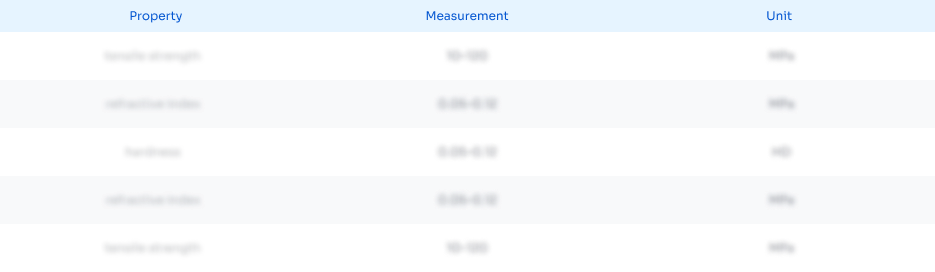
Abstract
Description
Claims
Application Information

- Generate Ideas
- Intellectual Property
- Life Sciences
- Materials
- Tech Scout
- Unparalleled Data Quality
- Higher Quality Content
- 60% Fewer Hallucinations
Browse by: Latest US Patents, China's latest patents, Technical Efficacy Thesaurus, Application Domain, Technology Topic, Popular Technical Reports.
© 2025 PatSnap. All rights reserved.Legal|Privacy policy|Modern Slavery Act Transparency Statement|Sitemap|About US| Contact US: help@patsnap.com