Method for preparing bio-ceramic film on surface of magnesium/magnesium alloy through micro-arc oxidation
A bioceramic membrane and micro-arc oxidation technology, which is applied in the field of medical metal implant materials, can solve problems such as unsatisfactory biocompatibility, and achieve good versatility, low cost, and improved corrosion resistance
- Summary
- Abstract
- Description
- Claims
- Application Information
AI Technical Summary
Problems solved by technology
Method used
Image
Examples
Embodiment 1
[0030] (1) Use deionized water as a solvent to prepare a phosphate and silicate composite system solution, containing 30 g of sodium phosphate, 10 g of sodium silicate, 5 g of calcium glycerophosphate, 5 g of potassium carbonate, 2 g of borax, and 2 g of hydrogen per liter of the composite system solution. Sodium oxide adjusts the pH value of the composite system solution to be 8, and then the composite system solution is placed in the electrolytic cell and left to stand for 24 hours as the electrolyte;
[0031] (2) Magnesium to be treated is placed in the electrolyte described in step (1) as an anode, the stainless steel plate is used as a cathode, the temperature of the control electrolyte is 10°C, and the pulse frequency of the micro-arc oxidation power supply (DC pulse power supply) is adjusted to 600Hz , the duty ratio is 15%, and the voltage is 350V under the condition of constant voltage treatment for 30min, that is, a layer of uniform and dense bioceramic film is grown ...
Embodiment 2
[0035] (1) Use deionized water as a solvent to prepare a phosphate and silicate composite system solution, containing 25 g of sodium phosphate, 10 g of sodium silicate, 10 g of calcium glycerophosphate, 10 g of potassium carbonate, 5 g of borax, and 5 g of hydrogen per liter of the composite system solution. Sodium oxide adjusts the pH value of the composite system solution to 10, and then the composite system solution is placed in the electrolytic cell and left for 24 hours as the electrolyte;
[0036](2) the magnesium alloy to be treated is placed in the electrolyte described in step (1) as an anode, the stainless steel plate is used as a cathode, the temperature of the control electrolyte is 15°C, and the pulse frequency of the micro-arc oxidation power supply (DC pulse power supply) is adjusted to 550Hz, duty ratio 20%, constant voltage treatment for 5min under the condition of voltage 350V, that is to grow a layer of uniform and dense bioceramic film on the surface of magn...
Embodiment 3
[0040] (1) Use deionized water as a solvent to prepare a phosphate and silicate composite system solution, containing 40 g of sodium phosphate, 2 g of sodium silicate, 30 g of calcium glycerophosphate, 1 g of potassium carbonate, 8 g of borax, and Sodium oxide adjusts the pH value of the composite system solution to 14, and then the composite system solution is placed in an electrolytic cell and left to stand for 24 hours as an electrolyte;
[0041] (2) Magnesium to be treated is placed in the electrolyte described in step (1) as an anode, the stainless steel plate is used as a cathode, the temperature of the control electrolyte is 45°C, and the pulse frequency of the micro-arc oxidation power supply (DC pulse power supply) is adjusted to 2000Hz , the duty ratio is 10%, and the voltage is 400V under the condition of constant voltage treatment for 3 minutes, that is, a layer of uniform and dense bioceramic film is grown in situ on the magnesium surface.
[0042] In this example...
PUM
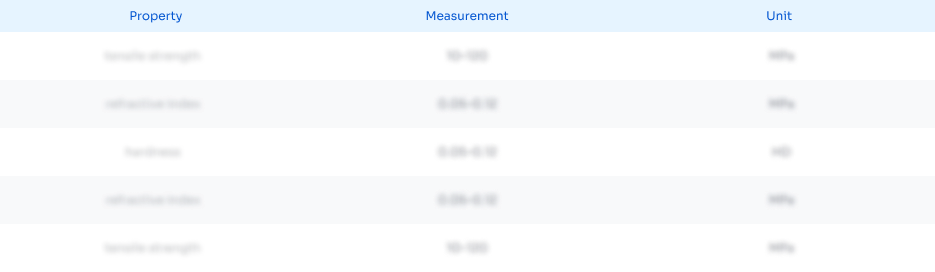
Abstract
Description
Claims
Application Information

- R&D
- Intellectual Property
- Life Sciences
- Materials
- Tech Scout
- Unparalleled Data Quality
- Higher Quality Content
- 60% Fewer Hallucinations
Browse by: Latest US Patents, China's latest patents, Technical Efficacy Thesaurus, Application Domain, Technology Topic, Popular Technical Reports.
© 2025 PatSnap. All rights reserved.Legal|Privacy policy|Modern Slavery Act Transparency Statement|Sitemap|About US| Contact US: help@patsnap.com