A system and method for variable speed winding of a square winder
A winding machine, variable speed technology, applied in sustainable manufacturing/processing, electrochemical generators, electrical components, etc., can solve the fluctuation of tension and the difficulty of debugging, affect battery quality and production efficiency, restrict winding Winding speed and other issues to achieve constant tension, reduce deformation, and improve quality
- Summary
- Abstract
- Description
- Claims
- Application Information
AI Technical Summary
Problems solved by technology
Method used
Image
Examples
Embodiment 1
[0037] Such as figure 1 As shown, this example provides a variable speed winding system for a square winding machine, including a servo motor module, an encoding module, an acquisition module, and a control module. The servo motor module includes a winding needle drive unit and a pulse generator unit. The winding needle driving unit adopts a servo motor to drive the winding needle 4, and the pulse generator unit is used to output the working pulse of the servo motor module;
[0038] The encoding module uses an encoder unit to regularly interrupt and output feedback pulses;
[0039] The collection module is used to simultaneously collect the working pulse and the feedback pulse;
[0040] The control module includes a central processing unit, a memory unit and a control unit, the central processing unit is used to calculate the winding speed corresponding to the feedback pulse, and store the corresponding relationship between the winding speed, the working pulse and the feedbac...
Embodiment 2
[0050] This example provides a winding method for the variable speed winding system of a square winder described in Embodiment 1, including a sampling step and a control step,
[0051] The sampling step is used to collect the working pulse and the feedback pulse at the same time, and drive the rolling needle 4 of the system at a constant speed. The pulse data of the feedback pulse is sent to the control step;
[0052] The control step forms a corresponding relationship between the received working pulse and the feedback pulse, and is used to control the winding speed of the system. The control step collects the current working pulse in real time, and maintains the current winding speed and the working pulse The corresponding winding speed is the same.
[0053] Wherein, the current working pulse is that the winding system of the square winding machine is in normal operation, that is, after the corresponding relationship is formed, the servo motor variable speed drives the wind...
Embodiment 3
[0056] The difference from Embodiment 2 is that in the sampling step described in this embodiment, the winding speed of the winding needle 4 of the system driven at a constant speed is 0.2 revolutions / second.
[0057] This example rotates at a low speed and constant speed in the sampling step, so that the feedback pulse output by the encoder unit can be stably obtained, and the winding speed of the winding needle 4 is 0.2 circles / second, which can obtain enough pulse data, and at the same time It saves the space of the memory unit and obtains an accurate corresponding relationship. On this basis, this example can effectively promote the winding at a uniform linear speed during the winding process, reduce the tension of the tape material, and largely avoid the winding process. The deformation of the battery core is neatly wound.
PUM
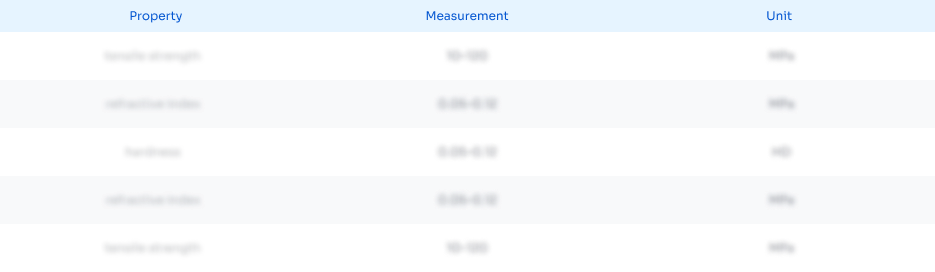
Abstract
Description
Claims
Application Information

- R&D Engineer
- R&D Manager
- IP Professional
- Industry Leading Data Capabilities
- Powerful AI technology
- Patent DNA Extraction
Browse by: Latest US Patents, China's latest patents, Technical Efficacy Thesaurus, Application Domain, Technology Topic, Popular Technical Reports.
© 2024 PatSnap. All rights reserved.Legal|Privacy policy|Modern Slavery Act Transparency Statement|Sitemap|About US| Contact US: help@patsnap.com