A kind of preparation method of copper-nickel-tin alloy
A copper-nickel-tin and alloy technology, applied in the field of copper-nickel-tin alloy preparation, can solve problems such as the difficulty in realizing the industrial production of copper-nickel-tin alloy plates and strips, achieve good plasticity, shorten the process flow, and save energy
- Summary
- Abstract
- Description
- Claims
- Application Information
AI Technical Summary
Problems solved by technology
Method used
Image
Examples
Embodiment 1
[0025] like figure 1 Shown, the copper-nickel-tin alloy preparation method of the present invention, concrete steps are:
[0026] 1. Melting ingot: use non-vacuum induction furnace for melting. The order of adding the alloy is: electrolytic copper, pure nickel, heating until the melt is completely melted, adding a covering agent (charcoal) and keeping it warm for 5-10 minutes, after degassing and impurity removal, and then covering with burning charcoal about 10mm thick. After heat preservation for 10 minutes, add dried Cu-P, Zn, Sn, fully stir, let stand for 5-10 minutes, and then cast out of the furnace. The casting temperature is 1200°C-1250°C.
[0027] 2. Solution treatment: the ingot is subjected to solution treatment in a heating furnace with protective gas, the solution temperature is 800°C, the holding time is 2-5h, and the cooling method is water cooling.
[0028] 3. Rough rolling: 80-85% rough rolling deformation of the solution-treated alloy.
[0029] 4. Interme...
Embodiment 2
[0036] 1. Melting ingot: use non-vacuum induction furnace for melting. The order of adding the alloy is: electrolytic copper, pure nickel, heating until the melt is completely melted, adding a covering agent (charcoal) and keeping it warm for 5-10 minutes, after degassing and impurity removal, and then covering with burning charcoal about 10mm thick. After heat preservation for 10 minutes, add dried Cu-P, Zn, Sn, fully stir, let stand for 5-10 minutes, and then cast out of the furnace. The casting temperature is 1200°C-1250°C.
[0037] 2. Solution treatment: the ingot is subjected to solution treatment in a heating furnace with protective gas, the solution temperature is 850°C, the holding time is 2-5h, and the cooling method is water cooling.
[0038] 3. Rough rolling: 80-85% rough rolling deformation of the solution-treated alloy.
[0039] 4. Intermediate annealing: Put the rough rolled alloy into the heat treatment annealing furnace for intermediate annealing, the anneali...
Embodiment 3
[0046] 1. Melting ingot: use non-vacuum induction furnace for melting. The order of adding the alloy is: electrolytic copper, pure nickel, heating until the melt is completely melted, adding a covering agent (charcoal) and keeping it warm for 5-10 minutes, after degassing and impurity removal, and then covering with burning charcoal about 10mm thick. After heat preservation for 10 minutes, add dried Cu-P, Zn, Sn, fully stir, let stand for 5-10 minutes, and then cast out of the furnace. The casting temperature is 1200°C-1250°C.
[0047] 2. Solution treatment: the ingot is subjected to solution treatment in a heating furnace with protective gas, the solution temperature is 900°C, the holding time is 2-5h, and the cooling method is water cooling.
[0048] 3. Rough rolling: 80-85% rough rolling deformation of the solution-treated alloy.
[0049] 4. Intermediate annealing: Put the rough rolled alloy into the heat treatment annealing furnace for intermediate annealing, the anneali...
PUM
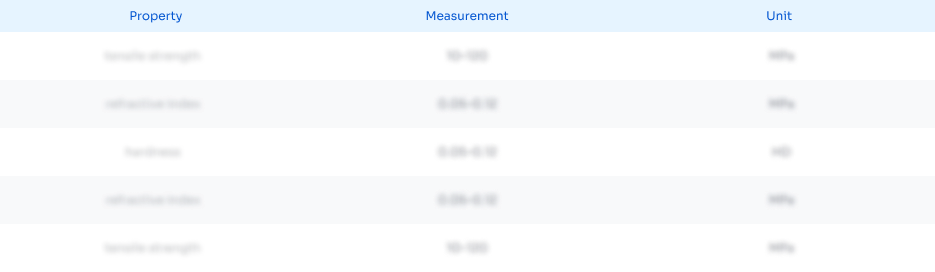
Abstract
Description
Claims
Application Information

- R&D
- Intellectual Property
- Life Sciences
- Materials
- Tech Scout
- Unparalleled Data Quality
- Higher Quality Content
- 60% Fewer Hallucinations
Browse by: Latest US Patents, China's latest patents, Technical Efficacy Thesaurus, Application Domain, Technology Topic, Popular Technical Reports.
© 2025 PatSnap. All rights reserved.Legal|Privacy policy|Modern Slavery Act Transparency Statement|Sitemap|About US| Contact US: help@patsnap.com