Grinding head spindle assembly for ball grinder with hollow cooling and flushing structure
A spindle and sphere technology, applied in the field of the grinding head spindle assembly of a ball grinder, can solve the problems of poor surface quality of grinding spheres, inability to achieve cooling and flushing effect, and single cooling liquid supply method, and improve machining accuracy and stability. , Solve the effect of thermal stability and poor grinding surface quality
- Summary
- Abstract
- Description
- Claims
- Application Information
AI Technical Summary
Problems solved by technology
Method used
Image
Examples
Embodiment Construction
[0012] Attached below figure 1 , 2 , 3 describe an embodiment of the present invention.
[0013] A ball grinder grinding head spindle assembly with a hollow cooling and flushing structure, comprising a grinding disc 1, a bearing I3, a bearing II6, a sleeve 4, a main shaft 5 and a pulley 7, the main shaft 5 is installed on the In the sleeve 4, the belt pulley 7 and the grinding disc 1 are respectively fixed on the two ends of the main shaft 5. The center of the main shaft 5 has an axial through hole 9, the rear end of the main shaft 5 is connected with a rotary joint 8, the front end of the main shaft 5 is connected with a hydraulic spray disc 2, and the hydraulic spray disc 2 is fixed in the center of the inner cavity of the grinding disc 1, and The liquid inlet port of the hydraulic injection disc 2 communicates with the front end of the axial through hole 9 , and the inner chamber of the rotary joint 8 communicates with the rear end of the axial through hole 9 .
[0014] ...
PUM
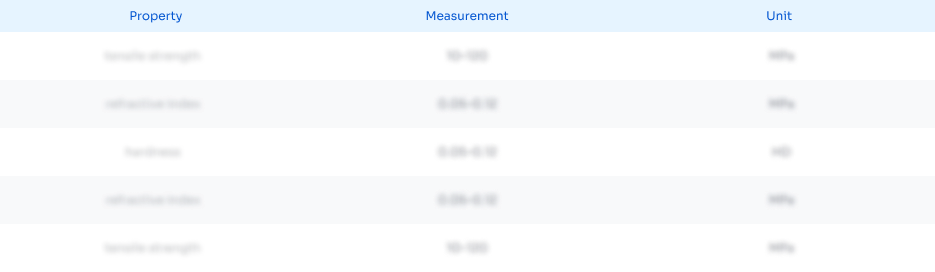
Abstract
Description
Claims
Application Information

- R&D Engineer
- R&D Manager
- IP Professional
- Industry Leading Data Capabilities
- Powerful AI technology
- Patent DNA Extraction
Browse by: Latest US Patents, China's latest patents, Technical Efficacy Thesaurus, Application Domain, Technology Topic, Popular Technical Reports.
© 2024 PatSnap. All rights reserved.Legal|Privacy policy|Modern Slavery Act Transparency Statement|Sitemap|About US| Contact US: help@patsnap.com