Oil injection nozzle orifice quenching process
A processing technology and fuel injection nozzle technology, which is applied in the field of fuel injection nozzle nozzle hole quenching processing technology, can solve the problems that the fuel injection nozzle processing technology cannot meet the requirements, cannot meet high-end customers, and affect the performance of the engine, so as to achieve processing accuracy and stability. High performance, improve processing efficiency, and improve the effect of yield
- Summary
- Abstract
- Description
- Claims
- Application Information
AI Technical Summary
Problems solved by technology
Method used
Examples
Embodiment 1
[0023] Embodiment 1: A nozzle hole quenching process, comprising the following steps:
[0024] (1) Positioning and clamping: place the fuel injector on the injection hole machine tool, use positioning pins for spatial axial positioning, and clamp with a claw-shaped mechanism, the working range of which is -20-90°;
[0025] (2) EDM: The pulse frequency of the electrode wire is 130KHz, the discharge gap is 58% of the voltage, and the correction is performed, the correction length is 0.6mm, and the feed rate during EDM is 1 / 6 of the nozzle hole depth;
[0026] (3) Quenching treatment: Quenching treatment is carried out on the fuel injector after EDM, the treatment temperature is 180-210°, and then the oil is cooled to room temperature;
[0027] (4) Nozzle hole trimming: Remove the barbs from the electrode wire processed in step (2), and trim the quenched fuel injector in step (3). The gap is 60% voltage;
[0028] (5) Shifting and clamping: place the fuel injector processed in s...
PUM
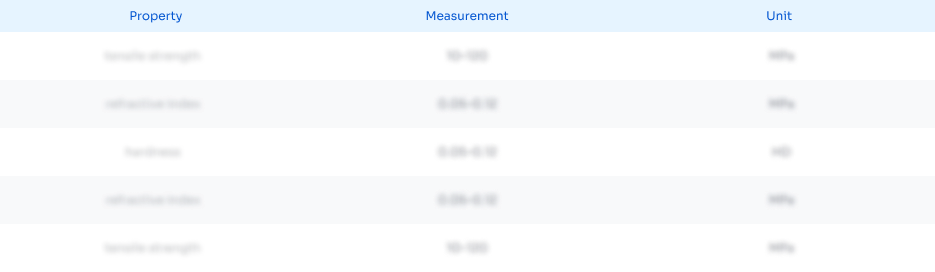
Abstract
Description
Claims
Application Information

- R&D Engineer
- R&D Manager
- IP Professional
- Industry Leading Data Capabilities
- Powerful AI technology
- Patent DNA Extraction
Browse by: Latest US Patents, China's latest patents, Technical Efficacy Thesaurus, Application Domain, Technology Topic, Popular Technical Reports.
© 2024 PatSnap. All rights reserved.Legal|Privacy policy|Modern Slavery Act Transparency Statement|Sitemap|About US| Contact US: help@patsnap.com