Structural and Morphological Control Method of Magnetic Abrasives Prepared by Gas Atomization Rapid Solidification
A technology of magnetic abrasives and control methods, applied in chemical instruments and methods, other chemical processes, etc., can solve the problems of difficult to control the particle size of hard abrasives, low content of ceramic hard abrasives, and incomparable grinding ability. The effect of enhanced, high permeability, and improved processing efficiency
- Summary
- Abstract
- Description
- Claims
- Application Information
AI Technical Summary
Problems solved by technology
Method used
Image
Examples
Embodiment 1
[0051] Embodiment 1: the magnetic abrasive material prepared by gas atomization fast setting method
[0052] The melting temperature of the metal body and the injection pressure of the mixed powder airflow are all within the parameter control range. The obtained magnetic abrasive has a regular spherical shape, and the hard abrasive is evenly distributed on the superficial layer of the metal body and firmly combined with the metal body. figure 2 , attached image 3 , attached Figure 4 , attached Figure 5 The structural morphology shown.
[0053] attached figure 2 , attached image 3 It shows that under the appropriate control parameters, the magnetic abrasive has a spherical structure, the hard abrasive is evenly distributed on the surface of the ferromagnetic metal body, the cutting edge protrudes outside, and the distance between the outermost cutting edge and the surface of the metal body is basically the same.
[0054] attached Figure 4 It is shown that the hard ...
Embodiment 2
[0057] The cross-sectional view of the morphology and structure of the magnetic abrasive prepared by the atomization quick-setting method under ideal process parameters is shown in the attached figure 1 shown. Embodiment 2: The impact of metal body melting temperature change on the morphology and structure of the prepared magnetic abrasive
[0058] (1) The injection pressure of the mixed powder airflow is moderate, and when the melting temperature of the metal body exceeds its melting point of 300°C, the shape of the magnetic abrasive is still a regular spherical shape, but due to the long cooling and solidification time, too much hard abrasive is free from the metal body And part of it falls off, making the combination of hard abrasive and metal body not firm enough, showing as attached Figure 6 The structural morphology shown.
[0059] (2) The injection pressure of the mixed powder airflow is moderate, and the melting temperature of the metal body is only 40°C higher than...
Embodiment 3
[0060] Example 3: The impact of the powder mixing air jet pressure change on the morphology and structure of the prepared magnetic abrasive
[0061] (1) The melting temperature of the metal body is moderate, and when the injection pressure of the powder-mixing airflow is as high as 4.0 MPa, the prepared magnetic abrasive is not only small, but also the combination of the hard abrasive and the metal body is not firm because the injection speed of the powder-mixing airflow is too high. Figure 8 The structural morphology shown.
[0062] (2) The melting temperature of the metal body is moderate, and when the injection pressure of the powder mixing airflow is only 0.5 MPa, the ferromagnetic metal cannot be atomized well because the injection speed of the powder mixing airflow is too low, and the formed magnetic abrasive is not only coarse, but not spherical , and the hard abrasive particles are only distributed on the surface of the metal body, and the combination with the metal b...
PUM
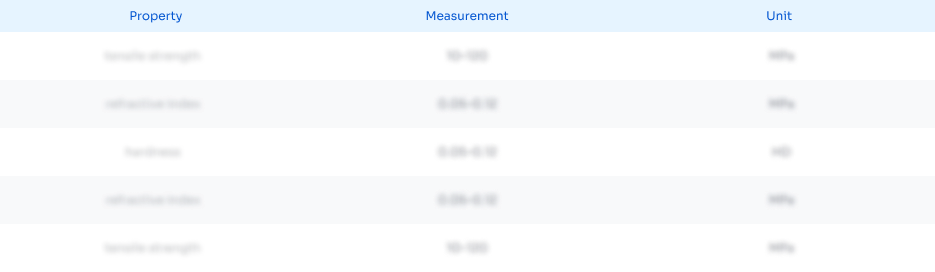
Abstract
Description
Claims
Application Information

- R&D Engineer
- R&D Manager
- IP Professional
- Industry Leading Data Capabilities
- Powerful AI technology
- Patent DNA Extraction
Browse by: Latest US Patents, China's latest patents, Technical Efficacy Thesaurus, Application Domain, Technology Topic, Popular Technical Reports.
© 2024 PatSnap. All rights reserved.Legal|Privacy policy|Modern Slavery Act Transparency Statement|Sitemap|About US| Contact US: help@patsnap.com