Manufacturing method of lattice core, mold and composite cylinder with lattice core
A composite material layer and core technology, which is applied in the field of composite material cylinders, can solve the problems of impenetrable space, inconvenient pre-embedding, heat conduction, ventilation and heat transfer, etc., and achieve the effect of perfect performance and easy pre-embedding
- Summary
- Abstract
- Description
- Claims
- Application Information
AI Technical Summary
Problems solved by technology
Method used
Image
Examples
specific Embodiment approach 1
[0030] Specific implementation mode one: combine Figure 1-Figure 12 Describe this embodiment, the concrete method of the preparation dot matrix core of this embodiment is as follows:
[0031] Step 1. Lay multiple sheet-shaped unidirectional prepregs superimposedly, and cut the stacked sheet-shaped unidirectional prepregs into strips with scissors or engraving machine according to the width of the square groove of the female mold in the mold, Obtain a unidirectional prepreg, the length of the unidirectional prepreg is 35-40mm longer than the length of the square groove of the first module, on the inner wall of the silicone rubber cylinder, evenly surround the prepreg, place in the steel mold and fixed at the bottom;
[0032] Step 2. Clean the outer surface of all the female molds in the mold and each mold body in the male mold, then apply the sealing agent and the release agent on the outer surface in turn, discharge the mold into a flat plate and bend it into a circle cylin...
specific Embodiment approach 2
[0038] Specific implementation mode two: combination Figure 1-Figure 12 To describe this embodiment, the curing temperature described in Step 5 of this embodiment is 120° C., the curing pressure is 0.5 MPa, and the curing time is 1.5 hours. With such setting, the curing effect is good. Other compositions and connections are the same as in the first embodiment.
specific Embodiment approach 3
[0039] Specific implementation mode three: combination Figure 1-Figure 7 Describe this embodiment, the mold of this embodiment is made up of female mold, male mold and splint 5, described female mold is made up of N first mold bodies 1, and described male mold is made up of N-1 second mold bodies 2. The third mold body 3 and the fourth mold body 4 are composed, the cross-sectional shape of the first mold body 1 is arc-shaped, the cross-sectional shape of the second mold body 2 is arc-shaped, and the third mold body 3 The cross-sectional shape of the fourth mold body 4 is fan-shaped; the first mold body 1 is composed of a first concave module 1-1, a second concave module 1-2 and a first intermediate module 1 -3 components, the cross-sectional shape of the first middle module 1-3 is isosceles trapezoid, the first concave module 1-1 and the second concave module 1-2 are symmetrically placed on the two sides of the first middle module 1-3 On the slope, on the surface of the firs...
PUM
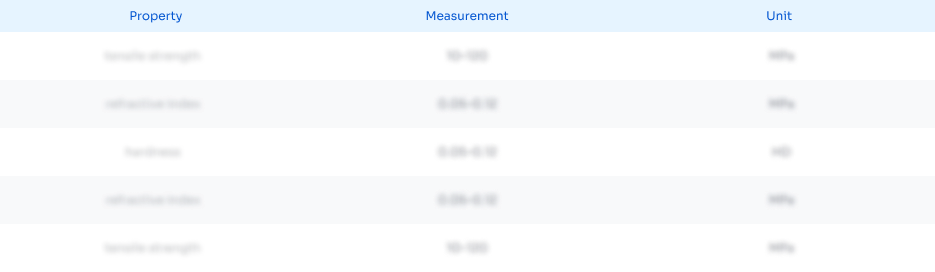
Abstract
Description
Claims
Application Information

- R&D
- Intellectual Property
- Life Sciences
- Materials
- Tech Scout
- Unparalleled Data Quality
- Higher Quality Content
- 60% Fewer Hallucinations
Browse by: Latest US Patents, China's latest patents, Technical Efficacy Thesaurus, Application Domain, Technology Topic, Popular Technical Reports.
© 2025 PatSnap. All rights reserved.Legal|Privacy policy|Modern Slavery Act Transparency Statement|Sitemap|About US| Contact US: help@patsnap.com