A kind of metal surface modification method
A metal surface modification technology, applied in metal material coating process, fusion spraying, coating, etc., can solve the problem of low energy conversion efficiency and achieve the effect of saving resources and energy
- Summary
- Abstract
- Description
- Claims
- Application Information
AI Technical Summary
Problems solved by technology
Method used
Image
Examples
Embodiment 1
[0027] A metal surface modification method, the metal surface is modified by surface texturing-powder spraying-laser remelting technology, comprising the following steps:
[0028] Texturize the treated metal surface with electron beams in vacuum to form tiny texturized pits with a diameter of 0.4mm and a depth of 0.2mm. The alloy powder is sprayed into the pits on the metal surface to be treated, the inert gas used for spraying and blowing is argon, its purity is 99.99%, the Co-based alloy powder is Stellite 6, and its chemical composition is shown in Table 1, and then the plasma arc is used to The blowing force mixes the molten base metal and nano-Co-based alloy powder evenly to form a dense and highly bonded melt-sprayed coating, and finally uses CO 2 The laser performs a single laser scan on the melt-sprayed coating, wherein the power is 2.0kW, the scanning speed is 2.0mm / s, and the spot diameter is 1.2mm, that is, the processed metal is obtained.
Embodiment 2
[0030] A metal surface modification method, the metal surface is modified by surface texturing-powder spraying-laser remelting technology, comprising the following steps:
[0031] Texturize the treated metal surface with electron beams in vacuum to form tiny texturized pits with a diameter of 0.2mm and a depth of 0.2mm. The powder is sprayed into the pits on the metal surface to be treated. The Co-based alloy powder is HMSP2528, and its chemical composition is shown in Table 1. The inert gas used for spraying and blowing is helium, and its purity is 99.99%. Mix the molten base metal and nano-Co-based alloy powder evenly to form a dense and high-strength melt-sprayed coating, and finally use CO 2 The laser performs a single laser scan on the melt-sprayed coating, wherein the power is 5.0kW, the scanning speed is 2.0mm / s, and the ratio of spot to diameter is 4.0mm, that is, the processed metal is obtained.
Embodiment 3
[0033] A metal surface modification method, the metal surface is modified by surface texturing-powder spraying-laser remelting technology, comprising the following steps:
[0034] Texturize the treated metal surface with electron beams in vacuum to form tiny texturized pits with a diameter of 0.3 mm and a depth of 0.1 mm. At the same time, nano-Co The base alloy powder is sprayed into the pits on the metal surface to be treated. The Co base alloy powder is HMSP2528, and its chemical composition is shown in Table 1. The inert gas used for spraying and blowing is helium, and its purity is 99.99%. The blowing force mixes the molten base metal and Co-based alloy powder evenly to form a dense and highly bonded melt-sprayed coating, and finally uses CO 2 The laser performs a single laser scan on the melt-sprayed coating, wherein the power is 4.0kW, the scanning speed is 15.0mm / s, and the ratio of spot to diameter is 4.0mm, that is, the processed metal is obtained.
PUM
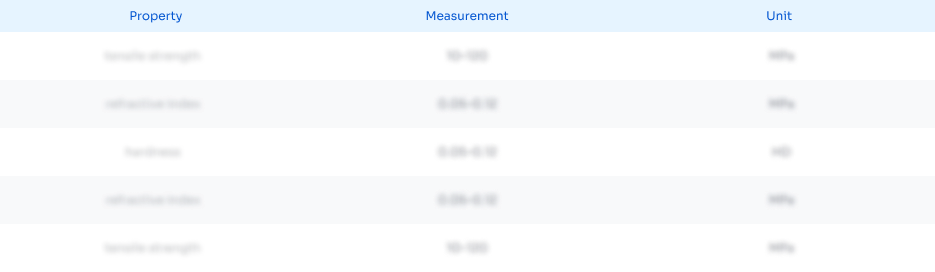
Abstract
Description
Claims
Application Information

- R&D
- Intellectual Property
- Life Sciences
- Materials
- Tech Scout
- Unparalleled Data Quality
- Higher Quality Content
- 60% Fewer Hallucinations
Browse by: Latest US Patents, China's latest patents, Technical Efficacy Thesaurus, Application Domain, Technology Topic, Popular Technical Reports.
© 2025 PatSnap. All rights reserved.Legal|Privacy policy|Modern Slavery Act Transparency Statement|Sitemap|About US| Contact US: help@patsnap.com