Mold for automatically cutting water port in mold of common injection molding machine through cold pulling
An injection molding machine and nozzle technology, applied in the field of plastic molds, can solve the problems of difficult manual shearing, easy scratching of plastic parts, high prices, etc., and achieve the effects of improving indirect benefits, improving average yield, and reducing production costs.
- Summary
- Abstract
- Description
- Claims
- Application Information
AI Technical Summary
Problems solved by technology
Method used
Image
Examples
Embodiment 1
[0058] This mold (such as figure 1 As shown, mold clamping state) is made up of static mold base 11, static template 6, movable mold base 19, movable template 14, mold foot 17, injection molding machine top stick 22 etc.
[0059] Below the static mold base 11 is the nozzle plate 8, and below the nozzle plate 8 is the static formwork 6. There is a groove in the static formwork 6, and a static mold core 13 is embedded in the groove. 21 is fixed with nozzle cutter 9, and is fixed with nozzle pin 10 in static mold seat 11, and the upper end of nozzle pin 10 is nozzle pin cup head 101, and the lower end is inverted cone head 102, and nozzle plate hole 81 is arranged in nozzle plate 8 , the nozzle pin 10 is fixed in the static mold seat 11 through the nozzle pin cup head 101, the nozzle pin 10 can slide in the nozzle plate hole 81, the inverted cone head 102 is used to connect the large nozzle 12, and there is Two static formwork large nozzle main channels 61, there are two static ...
Embodiment 2
[0065] This mold (such as Figure 4 As shown, mold clamping state) is made up of static mold base 11, static template 6, movable mold base 19, movable template 14, mold foot 17, injection molding machine top stick 22 etc.
[0066] Below the static mold base 11 is the nozzle plate 8, and below the nozzle plate 8 is the static template 6. There is a groove in the static template 6, and a static mold core 13 is embedded in the groove. There are two static mold cores 13. Right-angled nozzle cutter mounting groove, nozzle cutter 9 is installed in this installation groove, and this nozzle cutter 9 is made up of right-angled cutter body 98 and boss cutter head 95, and there is underflow channel 91 in the boss cutter head 95, in static mold seat 11 A nozzle pin 10 is fixed inside, the upper end of the nozzle pin 10 is a nozzle pin cup head 101, the lower end is an inverted cone head 102, there is a nozzle plate hole 81 in the nozzle plate 8, and the nozzle pin 10 passes through the no...
Embodiment 3
[0072] This mold (such as Figure 7 As shown, mold closing state) is composed of static mold base 11, static template 6, movable mold base 19, movable template 14, mold foot 17, injection molding machine top roller 22, etc.
[0073] Below the static mold base 11 is the nozzle plate 8, and below the nozzle plate 8 is the static template 6. There is a groove in the static template 6, and a static mold core 13 is embedded in the groove, and there is a place on the bottom surface of the static mold core 13. The nozzle cutter accommodating groove 51 of the right-angle nozzle cutter 9 is fixed with nozzle pin 10 in the static mold base 11, the nozzle pin 10 upper end is the nozzle pin cup head 101, and the lower end is an inverted cone head 102. There is a nozzle plate hole 81 inside, the nozzle pin 10 is fixed in the static mold base 11 through the nozzle pin cup head 101, the nozzle pin 10 can slide in the nozzle plate hole 81, and the inverted cone head 102 is used to connect the...
PUM
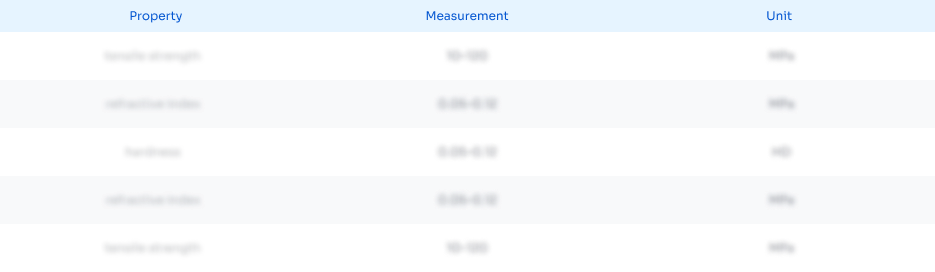
Abstract
Description
Claims
Application Information

- R&D
- Intellectual Property
- Life Sciences
- Materials
- Tech Scout
- Unparalleled Data Quality
- Higher Quality Content
- 60% Fewer Hallucinations
Browse by: Latest US Patents, China's latest patents, Technical Efficacy Thesaurus, Application Domain, Technology Topic, Popular Technical Reports.
© 2025 PatSnap. All rights reserved.Legal|Privacy policy|Modern Slavery Act Transparency Statement|Sitemap|About US| Contact US: help@patsnap.com