Method for controlling electronic pole inversion of multiphase induction motor on basis of vector control
A vector control, induction motor technology, applied in the direction of controlling electromechanical brakes, controlling generators, vector control systems, etc., can solve the problems of reduced control accuracy, economic and energy waste, and increased capacity of motor volume power devices.
- Summary
- Abstract
- Description
- Claims
- Application Information
AI Technical Summary
Problems solved by technology
Method used
Image
Examples
Embodiment Construction
[0061] The present invention will be further described below in conjunction with accompanying drawing.
[0062] A vector control-based electronic pole-changing control method for multi-phase induction motors proposed by the present invention, its principle block diagram is as follows figure 1 shown, including the following steps:
[0063] Such as figure 1 As shown, first establish the synchronous speed rotating coordinate transformation matrix of the multiphase system, as shown in formula (1), under this matrix by using n -1 current closed loop pair d1 -q 1 Fundamental current of the plane and other d-q The harmonic currents of the plane are independently decoupled and controlled, and the corresponding harmonic current vectors are respectively controlled by changing the phase and amplitude of the supply voltage to obtain the corresponding rotation of the rotating magnetic field.
[0064] (1)
[0065] In the formula: n is the number of phases of the motor ( n ≥3)...
PUM
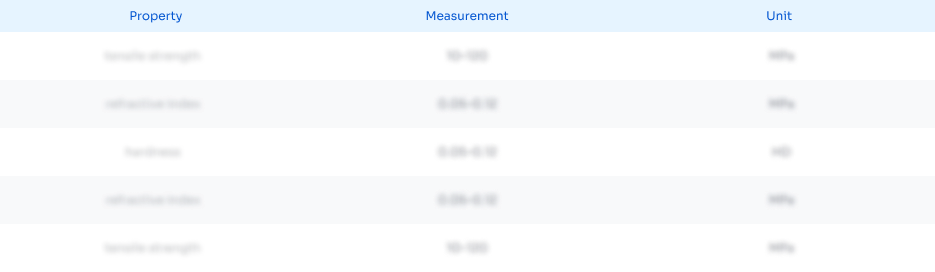
Abstract
Description
Claims
Application Information

- Generate Ideas
- Intellectual Property
- Life Sciences
- Materials
- Tech Scout
- Unparalleled Data Quality
- Higher Quality Content
- 60% Fewer Hallucinations
Browse by: Latest US Patents, China's latest patents, Technical Efficacy Thesaurus, Application Domain, Technology Topic, Popular Technical Reports.
© 2025 PatSnap. All rights reserved.Legal|Privacy policy|Modern Slavery Act Transparency Statement|Sitemap|About US| Contact US: help@patsnap.com