Cylindrical cam flapping wing driving mechanism
A technology of cylindrical cam and driving mechanism, which is applied in the field of miniature flapping wing aircraft, can solve the problems of complex control elements and feedback control systems, low aerodynamic efficiency, etc., and achieve the effects of improved stability, simple structure and light weight
- Summary
- Abstract
- Description
- Claims
- Application Information
AI Technical Summary
Problems solved by technology
Method used
Image
Examples
Embodiment Construction
[0022] The cylindrical cam flapping wing driving mechanism of the present invention comprises a frame 1, a motor 2, a gear reducer, a cylindrical cam mechanism and a rocker mechanism.
[0023] The frame 1 is a left-right symmetrical overall structure made of duralumin alloy numerical control processing. The bottom surface has a transmission shaft hole 1A and a motor mounting hole. The axes of the two are parallel, and they are all located in the symmetrical plane of the frame. The frame has a guide rail perpendicular to the bottom surface. A connecting rod 7 parallel to the guide rail and capable of sliding in the guide rail is installed in the guide rail. There are left and right symmetrical rocker shaft holes on both sides of the guide rail. Coaxial No. 2 transmission shaft hole 1B. There are fixing holes at the rear and top of the frame, which are installed on the support frame of the flapping-wing aircraft fuselage by screws or pins.
[0024] The DC brushless motor 2 is i...
PUM
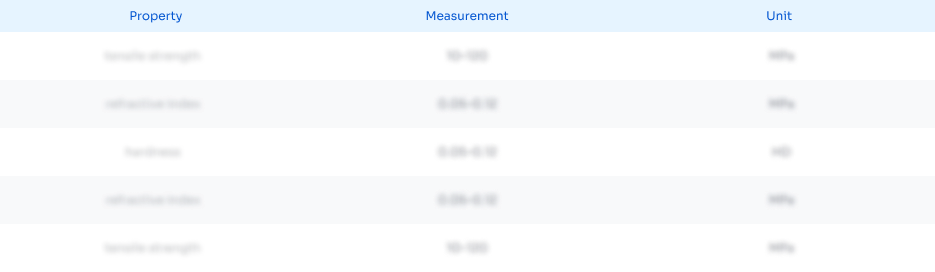
Abstract
Description
Claims
Application Information

- R&D Engineer
- R&D Manager
- IP Professional
- Industry Leading Data Capabilities
- Powerful AI technology
- Patent DNA Extraction
Browse by: Latest US Patents, China's latest patents, Technical Efficacy Thesaurus, Application Domain, Technology Topic, Popular Technical Reports.
© 2024 PatSnap. All rights reserved.Legal|Privacy policy|Modern Slavery Act Transparency Statement|Sitemap|About US| Contact US: help@patsnap.com