Method for preparing aluminum-scandium master alloy by thermal reduction of aluminum-calcium alloy
An aluminum-calcium alloy and master alloy technology is applied in the field of aluminum-scandium master alloy preparation, and achieves the effects of simple operation, low production energy consumption, and simple and feasible technological process.
- Summary
- Abstract
- Description
- Claims
- Application Information
AI Technical Summary
Problems solved by technology
Method used
Image
Examples
Embodiment 1
[0027] The invention discloses a method for preparing an aluminum-scandium master alloy by thermal reduction of an aluminum-calcium alloy, comprising:
[0028] 1) Calculate the weight of the raw materials aluminum-calcium alloy, scandium halide or its molten salt and alkali metal chloride required for each furnace smelting according to the composition content of the aluminum-scandium master alloy, and weigh them respectively;
[0029] 2) Mix scandium halide or its molten salt and alkali metal chloride evenly into the crucible and heat up to 750°C~950°C to melt to obtain molten scandium-containing molten salt;
[0030] 3) adding the aluminum-calcium alloy into the molten scandium-containing molten salt, and after the aluminum-calcium alloy is melted, heat-reduce for 20-200 minutes;
[0031] 4) After the thermal reduction reaction is completed, add excess refining agent to remove calcium, and when the calcium content in the alloy is less than 50ppm, pour the ingot and cool it, a...
Embodiment 2
[0034] On the basis of Example 1, the best implementation mode of the present invention is: in the aluminum-calcium alloy, the calcium content is 3% to 20% by weight, and the balance is aluminum and unavoidable impurities. Scandium halides are anhydrous scandium halides or scandium-containing molten salts prepared by chemical methods, and the anhydrous scandium halides are anhydrous scandium chloride, anhydrous scandium fluoride, anhydrous scandium bromide or anhydrous scandium iodide , requires complete dehydration, scandium halide content of 1% to 25% of the molten salt. The alkali metal halide is one or two mixtures of sodium chloride and potassium chloride, the weight ratio of sodium chloride and potassium chloride in the mixture is: 75-98:25-2, the amount of alkali metal halide is 0.1~1.5 times the weight of aluminum-calcium alloy. The crucible is graphite crucible, corundum crucible, iron crucible or tantalum crucible. The refining agent is a refining slag system compo...
Embodiment 3
[0037] Weigh 42.6g of sodium chloride, 42.6g of potassium chloride, and 10.6g of scandium fluoride, mix them evenly and add them into a graphite crucible, heat up to 800°C, and add 213.0g of aluminum-calcium alloy with a calcium content of 3.2% after the molten salt melts, After the aluminum-calcium alloy is melted, heat-reduce and smelt for 20 minutes, add 4% aluminum-calcium alloy refining agent to heat-reduce and decalcify for 30 minutes, take out the crucible, remove slag, cast and demould, and cool with water at 60-100°C. 212.3 g of aluminum-scandium master alloy was obtained by weighing after removing slag, and analyzed by ICP-AES, the scandium content was 2.06%, and the recovery rate of scandium was 93.2%. The contents of other impurities Ca, Na, F, etc. are all less than 50ppm. Slag recycling.
PUM
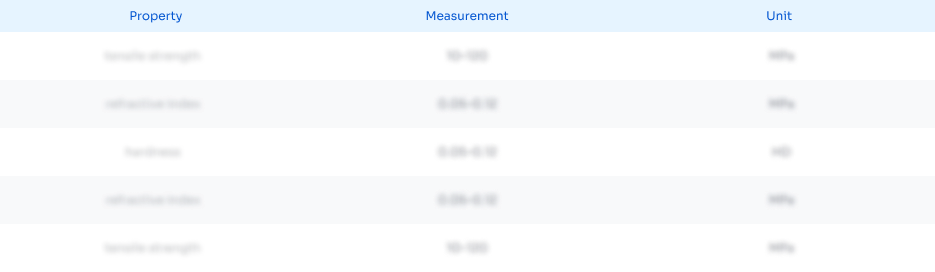
Abstract
Description
Claims
Application Information

- Generate Ideas
- Intellectual Property
- Life Sciences
- Materials
- Tech Scout
- Unparalleled Data Quality
- Higher Quality Content
- 60% Fewer Hallucinations
Browse by: Latest US Patents, China's latest patents, Technical Efficacy Thesaurus, Application Domain, Technology Topic, Popular Technical Reports.
© 2025 PatSnap. All rights reserved.Legal|Privacy policy|Modern Slavery Act Transparency Statement|Sitemap|About US| Contact US: help@patsnap.com