Nano composite modified melamine-formaldehyde abrasion-resisting resin and preparation method thereof
A melamine formaldehyde and nanocomposite technology, applied in building structure, paper, construction and other directions, can solve the problems of insufficient wear resistance, cost reduction, shortened storage period, etc., and achieve good wear resistance, clear and stable patterns good effect
- Summary
- Abstract
- Description
- Claims
- Application Information
AI Technical Summary
Problems solved by technology
Method used
Examples
preparation example Construction
[0023] In the preparation method, the reaction kettle adopts a reaction kettle with controllable temperature and a stirrer, the stirring speed used in steps ①②③④⑤ is 60-80 rpm, and the stirring speed used in step ⑥ is 100-200 rpm; the reaction time For: step ③ 80-100 minutes, step ④ 20-30 minutes, step ⑤ 20-30 minutes, step ⑥ 20-30 minutes.
[0024] The present invention is further clarified in conjunction with the following specific examples, but the present invention is not limited thereto.
Embodiment 1
[0026] Mix nano-alumina and nano-silicon dioxide at a mass ratio of 1:1 to form a nano-composite, and set aside; mix ethanol and diethylene glycol at a volume ratio of 2:1, set aside; 30 parts of water and 150 parts of formaldehyde with a concentration of 37% were added to the reaction kettle, and at the same time, the speed of the agitator was controlled at 65 rpm, and the pH was adjusted to 8.9 with an appropriate amount of 10% sodium hydroxide solution, and the temperature began to rise to 68 ℃, heat preservation and stirring for 5 minutes; at the end of heat preservation, add 100 parts of melamine, start to heat up to 85 ℃, heat preservation and stirring for 96 minutes; then add 43 parts of a mixture of ethanol and diethylene glycol, and continue to react for 25 minutes; then add 0.2 parts of polyacrylamide, Continue to react for 30 minutes; then add 20 parts of the nanocomposite, control the stirrer speed to 160 rpm, continue to stir for 20 minutes, and lower the temperatu...
Embodiment 2
[0028] Nano-alumina and nano-silicon dioxide treated with coupling agent KH-550 are made into a nano-composite at a mass ratio of 2:1 for later use; respectively add 100 parts of water, 200 parts of formaldehyde with a concentration of 36%, while controlling the speed of the agitator to 80 rpm, adjusting the pH to 9.1 with an appropriate amount of 20% sodium carbonate solution, starting to heat up to 60°C, and stirring for 10 minutes; after the heat preservation, add 120 30 parts of melamine, began to heat up to 92 ° C, and kept stirring for 80 minutes; then added 30 parts of glycerol and continued to react for 20 minutes; then added 2 parts of sodium carboxymethyl cellulose and continued to react for 22 minutes; then added 30 parts of nanocomposites to control The rotation speed of the stirrer is 100 rpm, and the stirring is continued for 25 minutes, and the temperature is lowered to below 40° C. to prepare the nanocomposite modified melamine formaldehyde wear-resistant resin....
PUM
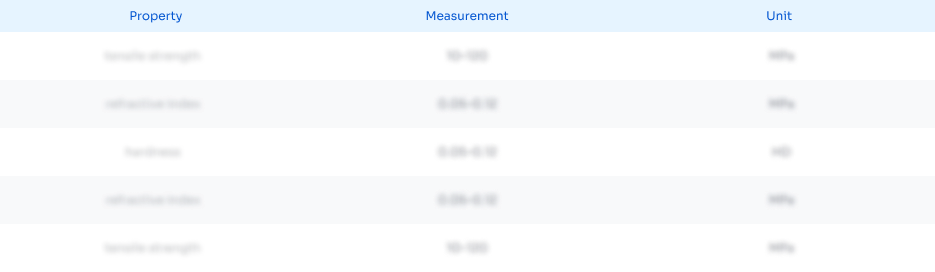
Abstract
Description
Claims
Application Information

- Generate Ideas
- Intellectual Property
- Life Sciences
- Materials
- Tech Scout
- Unparalleled Data Quality
- Higher Quality Content
- 60% Fewer Hallucinations
Browse by: Latest US Patents, China's latest patents, Technical Efficacy Thesaurus, Application Domain, Technology Topic, Popular Technical Reports.
© 2025 PatSnap. All rights reserved.Legal|Privacy policy|Modern Slavery Act Transparency Statement|Sitemap|About US| Contact US: help@patsnap.com