Plastic extruding machine with curve-shaped machine neck flow channel
A curved and extruder technology, applied in the field of cable production, can solve problems such as uneven temperature, slow flow rate of polymer melt, and easy to produce dead edges on the flow channel wall.
- Summary
- Abstract
- Description
- Claims
- Application Information
AI Technical Summary
Problems solved by technology
Method used
Image
Examples
Embodiment Construction
[0013] Such as figure 2 , The extruder of the present invention has a curved neck runner, the longitudinal cross-sectional shape of the neck runner is curved, and the curve is:
[0014] (1) The neck runner adopts y=ax 2 function.
[0015] (2) The constant a is determined by the diameter of the screw barrel of the fuselage and the aperture of the nose inflow, specifically a= (Note: R Is the arc radius of the horn; D Large diameter of the horn, that is, the inner diameter of the body barrel; d It is the small diameter of the horn, that is, the diameter of the hole that flows into the nose).
[0016] (3) The flared edge is round and smooth (circular radius R ), take the circumference , No dead ends.
[0017] (4) The starting point to the end point of the entire trumpet curve is accurately positioned, and there is no dead point in surface processing.
[0018] The present invention provides an idea and implementation method for an extruder with a curvilinear neck runner. There are ma...
PUM
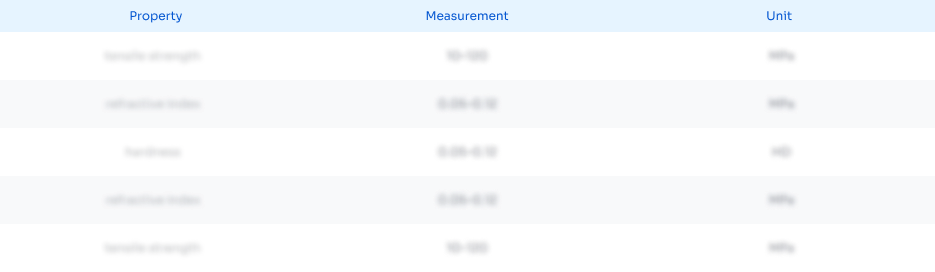
Abstract
Description
Claims
Application Information

- R&D Engineer
- R&D Manager
- IP Professional
- Industry Leading Data Capabilities
- Powerful AI technology
- Patent DNA Extraction
Browse by: Latest US Patents, China's latest patents, Technical Efficacy Thesaurus, Application Domain, Technology Topic, Popular Technical Reports.
© 2024 PatSnap. All rights reserved.Legal|Privacy policy|Modern Slavery Act Transparency Statement|Sitemap|About US| Contact US: help@patsnap.com