Numerical control system and control method based on dual-core architecture teamwork
A numerical control system and collaborative work technology, applied in the direction of total factory control, total factory control, electrical program control, etc., can solve the problems of low processing efficiency, system instability, CPU competition, etc., and achieve the goal of improving processing efficiency and fast transmission rate Effect
- Summary
- Abstract
- Description
- Claims
- Application Information
AI Technical Summary
Problems solved by technology
Method used
Image
Examples
Embodiment Construction
[0045] The detailed problems involved in the technical solutions of the present invention will be described in detail below with reference to the accompanying drawings. It should be noted that the described embodiments are only intended to facilitate the understanding of the present invention without any limitation thereto.
[0046] like figure 1The numerical control system structure based on the dual-core architecture is shown, including: a first logic unit 1, a second logic unit 2 and an AND gate 3, the first logic unit 1 and the second logic unit 2 are connected through an address bus and a data bus, and the An AND gate 3 is connected between an output end of the first logic unit 1 and an output end of the second logic unit 2; the input signal of the AND gate 3 is the control signal of the first logic unit 1 and the second logic unit 2 The output of the AND gate 3 is the synchronous control signal; when the machining starts, the first logic unit 1 first sets the control si...
PUM
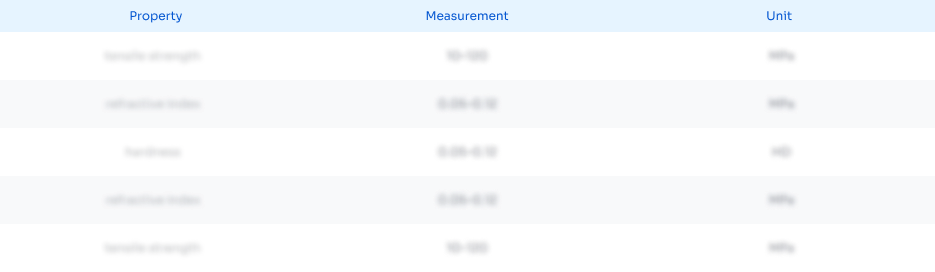
Abstract
Description
Claims
Application Information

- R&D
- Intellectual Property
- Life Sciences
- Materials
- Tech Scout
- Unparalleled Data Quality
- Higher Quality Content
- 60% Fewer Hallucinations
Browse by: Latest US Patents, China's latest patents, Technical Efficacy Thesaurus, Application Domain, Technology Topic, Popular Technical Reports.
© 2025 PatSnap. All rights reserved.Legal|Privacy policy|Modern Slavery Act Transparency Statement|Sitemap|About US| Contact US: help@patsnap.com