Method for confirming shrinkage of automobile part subjected to injection molding
An auto parts and injection molding technology, which is applied in the field of auto parts injection molding, can solve the problems that craftsmen have no experience to refer to, new materials have no experience to use, and the range is large and difficult to select, so as to reduce quality costs and improve project development capabilities. , The effect of reducing waste
- Summary
- Abstract
- Description
- Claims
- Application Information
AI Technical Summary
Problems solved by technology
Method used
Image
Examples
Embodiment
[0022] The present invention has been tested on the grille of Shanghai GM SGM411, which is made of ABSX17 plastic. First, engrave the size coordinates on the mold, and compare the actual product and mold coordinates through trial runs, confirm the shrinkage rate of this structure and this material. SGM411 grille has experienced non-shrinkage rate in the previous development process. To be accurate, use this method to mark the size points on the mold that has been opened, and measure the position after cooling to confirm the shrinkage.
[0023] Moreover, this method used a new PC+ABS material for the Shanghai GM 818 model, which also confirmed its shrinkage rate.
PUM
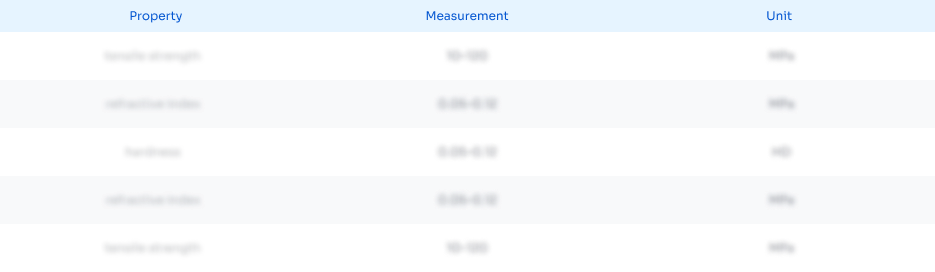
Abstract
Description
Claims
Application Information

- Generate Ideas
- Intellectual Property
- Life Sciences
- Materials
- Tech Scout
- Unparalleled Data Quality
- Higher Quality Content
- 60% Fewer Hallucinations
Browse by: Latest US Patents, China's latest patents, Technical Efficacy Thesaurus, Application Domain, Technology Topic, Popular Technical Reports.
© 2025 PatSnap. All rights reserved.Legal|Privacy policy|Modern Slavery Act Transparency Statement|Sitemap|About US| Contact US: help@patsnap.com