Method for manufacturing grinding wheel work layer with abrasive particle dressing function
A manufacturing method and technology of working layers, applied in grinding devices, manufacturing tools, metal processing equipment, etc., can solve the problems of adverse effects of workpiece materials, rising grinding temperature, and inability to maintain sharpness for a long time
- Summary
- Abstract
- Description
- Claims
- Application Information
AI Technical Summary
Problems solved by technology
Method used
Image
Examples
Embodiment 1
[0026] Example 1: The raw materials used are Cu-Sn-Ti alloy powder 1 (the mass ratio of Cu, Sn, and Ti elements is 7:2:1), polycrystalline cubic boron nitride PCBN abrasive grain 2 (CBN microcrystal 5 and The mass ratio of AlN binder 4 is 9:1), and submicron TiC particles 3 (100nm~5μm). Among them, polycrystalline cubic boron nitride PCBN abrasive particles 2 account for 10% of the total mass of raw materials, TiC particles 3 account for 10% of the total mass of raw materials, and the rest is Cu-Sn-Ti alloy powder. The mixture of the above raw materials is mechanically stirred and put into a powder tablet press to be pressed into a blank, and then vacuum liquid phase sintering is carried out at a heating temperature of 880°C and a holding time of 30 minutes, so that the Ti in the Cu-Sn-Ti alloy The elements react chemically with the CBN microcrystalline particles 5 and the AlN binder 4 in the polycrystalline cubic boron nitride PCBN abrasive grains 2 respectively, firmly hold ...
Embodiment 2
[0027] Example 2: The raw materials used are Cu-Sn-Ti alloy powder 1 (the mass ratio of Cu, Sn, and Ti elements is 7:2:1), polycrystalline cubic boron nitride PCBN abrasive grain 2 (CBN microcrystal and AlN The mass ratio of binder 4 is 9:1), and submicron TiC particles 3 (100nm~5μm). Among them, polycrystalline cubic boron nitride PCBN abrasive particles 2 account for 20% of the total mass of raw materials, TiC particles 3 account for 5% of the total mass of raw materials, and the rest are Cu-Sn-Ti alloy powder. The mixture of the above raw materials is mechanically stirred and put into a powder tablet press to be pressed into a blank, and then vacuum liquid phase sintering is carried out at a heating temperature of 940°C and a holding time of 10 minutes, so that the Ti in the Cu-Sn-Ti alloy The elements react chemically with the CBN microcrystalline particles 5 and the AlN binder 4 in the polycrystalline cubic boron nitride PCBN abrasive grains 2 respectively, firmly hold th...
Embodiment 3
[0028] Example 3: The raw materials used are Cu-Sn-Ti alloy powder 1 (the mass ratio of Cu, Sn, and Ti elements is 7:2:1), polycrystalline cubic boron nitride PCBN abrasive grain 2 (CBN microcrystal and AlN The mass ratio of binder 4 is 9:1), and submicron TiC particles 3 (100nm~5μm). Among them, polycrystalline cubic boron nitride PCBN abrasive grain 2 accounts for 10% of the total mass of raw materials, TiC particles account for 10% of the total mass of raw materials, and the rest is Cu-Sn-Ti alloy powder. The mixture of the above raw materials is mechanically stirred and put into a powder tablet press to form a blank, and then vacuum liquid phase sintering is carried out at a heating temperature of 940°C and a holding time of 10 minutes, so that the Cu-Sn-Ti alloy 1 The Ti element chemically reacts with the CBN microcrystalline particles 5 and the AlN binder 4 in the polycrystalline cubic boron nitride PCBN abrasive grains 2 respectively, firmly holds the polycrystalline cu...
PUM
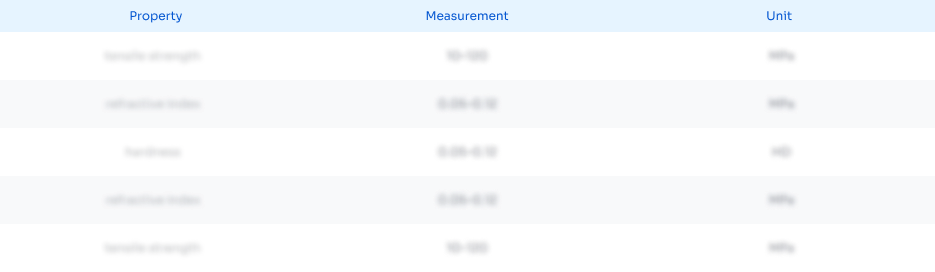
Abstract
Description
Claims
Application Information

- Generate Ideas
- Intellectual Property
- Life Sciences
- Materials
- Tech Scout
- Unparalleled Data Quality
- Higher Quality Content
- 60% Fewer Hallucinations
Browse by: Latest US Patents, China's latest patents, Technical Efficacy Thesaurus, Application Domain, Technology Topic, Popular Technical Reports.
© 2025 PatSnap. All rights reserved.Legal|Privacy policy|Modern Slavery Act Transparency Statement|Sitemap|About US| Contact US: help@patsnap.com