High-precision aluminum alloy rectangular tube forming method
A rectangular tube and aluminum alloy technology, which is applied in the field of forming high-precision aluminum alloy rectangular tubes, can solve problems such as tube blank breaking and corner transverse cracks, and achieve the effects of eliminating transverse cracks, compact structure, and excellent mechanical properties
- Summary
- Abstract
- Description
- Claims
- Application Information
AI Technical Summary
Problems solved by technology
Method used
Image
Examples
Embodiment
[0034] In this embodiment, an aluminum alloy tube with a height H and a width B ratio of 1:2.0, a size of 90.12mm×45.16mm×2.06mm, and an inner surface roughness of Ra1.0 as an example, proposes a method for manufacturing this type of rectangular tube The specific implementation steps are as follows:
[0035] a) Heat the prepared aluminum alloy ingot with the grade of 6061 to 415±5℃ for 1-2h. The purpose of the ingot homogenization treatment is to eliminate the residual stress formed inside the metal after the end of the metal casting, improve the plastic processing ability of the metal ingot, improve the structure and mechanical properties of the product, and prepare for the subsequent further processing. In actual production, most aluminum alloy ingots must be homogenized before pressure processing.
[0036] b) First, preheat the extrusion split die to 400°C, then put the aluminum alloy ingot with a heating temperature of 450°C into the extrusion barrel of the die, and the extrus...
PUM
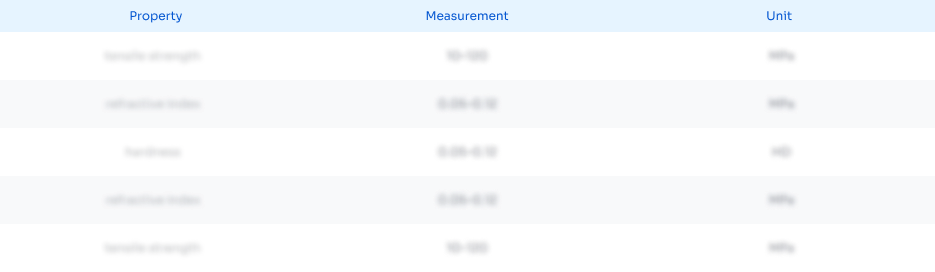
Abstract
Description
Claims
Application Information

- Generate Ideas
- Intellectual Property
- Life Sciences
- Materials
- Tech Scout
- Unparalleled Data Quality
- Higher Quality Content
- 60% Fewer Hallucinations
Browse by: Latest US Patents, China's latest patents, Technical Efficacy Thesaurus, Application Domain, Technology Topic, Popular Technical Reports.
© 2025 PatSnap. All rights reserved.Legal|Privacy policy|Modern Slavery Act Transparency Statement|Sitemap|About US| Contact US: help@patsnap.com