Torsion fiber optic acceleration transducer
An acceleration sensor and sensor technology, which is applied in the direction of using optical devices to transmit sensing components and using inertial force for acceleration measurement, etc., can solve the problems of temperature compensation restricting the development of optical fiber sensors, low measurement frequency, and inability to cover the frequency range of traditional acceleration sensors. , to achieve the effect of stable and reliable layout, wide linear range, and improved linearity and stability
- Summary
- Abstract
- Description
- Claims
- Application Information
AI Technical Summary
Problems solved by technology
Method used
Image
Examples
Embodiment Construction
[0018] Embodiments of the present invention will be described in detail below in conjunction with the accompanying drawings.
[0019] See attached figure 1 As shown, this kind of torsional differential temperature-compensated optical fiber acceleration sensor, at the midpoint of the elastic torsion shaft 1 fixed at both ends and the shell, uses the coaxial rotating disk 3 to connect and fix the mass block 2, and the mass block 2 is installed on the rotating On the disk 3, and the optical fiber with prestress is wound on the rotating disk 3, the fiber gratings 5 and 7 of the two suspended sections have the same length and prestress, and their other ends are fixed on the same axis as the torsion shaft 1 and the rotating disk 3. The optical fiber of the shaft is installed on the ring 4, and the signal is continuously connected to the demodulation instrument 8 through the optical fiber, and the optical fiber installation ring 4 is connected with the sensor housing by installing ...
PUM
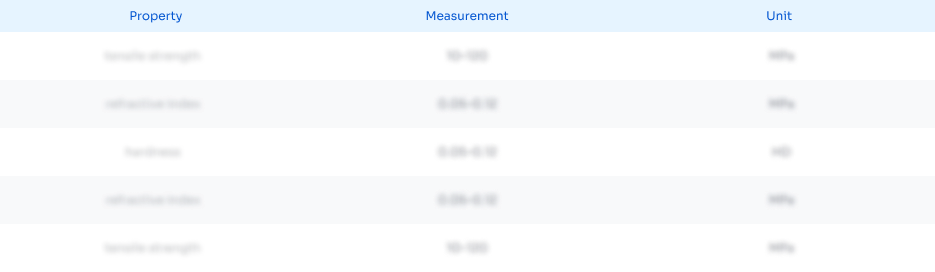
Abstract
Description
Claims
Application Information

- R&D
- Intellectual Property
- Life Sciences
- Materials
- Tech Scout
- Unparalleled Data Quality
- Higher Quality Content
- 60% Fewer Hallucinations
Browse by: Latest US Patents, China's latest patents, Technical Efficacy Thesaurus, Application Domain, Technology Topic, Popular Technical Reports.
© 2025 PatSnap. All rights reserved.Legal|Privacy policy|Modern Slavery Act Transparency Statement|Sitemap|About US| Contact US: help@patsnap.com