Rotor of built-in permanent magnet motor and magnetic steel structural parameter determining method thereof
A permanent magnet motor, built-in technology, applied in the shape/style/structure of the magnetic circuit, rotating parts of the magnetic circuit, etc., can solve the performance indicators affecting the torque ripple, vibration and noise efficiency of the motor, and the difficulty of the maximum safe running speed of the motor. The problems such as the increase of air gap flux density and the difficulty of adjusting the sine degree of the waveform to achieve the effect of increasing the maximum safe running speed, reducing the radial thickness and reducing the moment of inertia
- Summary
- Abstract
- Description
- Claims
- Application Information
AI Technical Summary
Problems solved by technology
Method used
Image
Examples
Embodiment 1
[0049] The high-quality high-speed built-in 4-pole permanent magnet motor rotor includes a rotor core (3) and a magnetic steel (1) built into it, and is characterized in that:
[0050] (1) The magnetic steel (1) of each pole is composed of odd-numbered magnetic steels of the same polarity;
[0051](2) The odd-numbered magnets of each pole are respectively built into the rotor core (3) along the rotor circumference; the centerline of the middle section of the magnet coincides with the centerline of the pole, and the remaining even-numbered magnets are symmetrically distributed on both sides. The size of the magnetic steel at the laterally symmetrical position is the same; a reinforcing rib (2) with a magnetic isolation effect is arranged between each adjacent two sections of the magnetic steel;
[0052] (3) The width of the magnets (1) with odd numbers of poles is modulated and determined according to the principle of the sinusoidal distribution of the air-gap magnetic density ...
Embodiment 2
[0055] This embodiment is basically the same as Embodiment 1, and the feature is that the magnetic poles are divided into 5 sections. Compared with the conventional structure, each pole is composed of 5 sections of magnetic steel (1a, 1b, 1c, 1d, 1e) of the same polarity, which are respectively built into the rotor core (3) along the circumference of the rotor, and the middle section of magnetic steel (1c ) coincides with the pole centerline, the magnets (1b, 1d) and the magnets (1a, 1e) are symmetrically distributed on both sides of the magnet (1c), the magnets (1b) and the magnets (1d), magnets The steel (1a) and the magnetic steel (1e) have the same size, and magnetic isolation reinforcing ribs (2a, 2b, 2c, 2d) are arranged between each section of the magnetic steel, and the distance between the magnetic steel (1a, 1e) and the outer circle of the rotor There are magnetic isolation bridges (4a, 4b) between them, and there are gaps between them and adjacent magnetic poles of ...
PUM
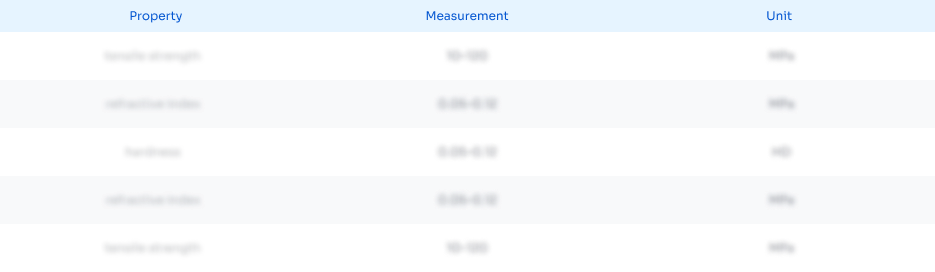
Abstract
Description
Claims
Application Information

- R&D
- Intellectual Property
- Life Sciences
- Materials
- Tech Scout
- Unparalleled Data Quality
- Higher Quality Content
- 60% Fewer Hallucinations
Browse by: Latest US Patents, China's latest patents, Technical Efficacy Thesaurus, Application Domain, Technology Topic, Popular Technical Reports.
© 2025 PatSnap. All rights reserved.Legal|Privacy policy|Modern Slavery Act Transparency Statement|Sitemap|About US| Contact US: help@patsnap.com