Vacuum degree gas saving regulation system
A technology for adjusting the system and vacuum degree, applied in the field of molten steel refining outside the furnace, can solve the problems of inability to adjust, increase the cost, unfavorable process flow, etc., and achieve good economic benefits, shorten the processing time, and save the effect of working steam.
- Summary
- Abstract
- Description
- Claims
- Application Information
AI Technical Summary
Problems solved by technology
Method used
Image
Examples
Embodiment 1
[0019] figure 1 , 2 A four-stage vacuum pump embodiment is given, including: the first booster pump 1, the second booster pump 2, the first condenser 3, the second condenser 4, the third condenser 5, the first jet pump 6 and the second jet Pump 7 and first auxiliary jet pump 8, second auxiliary jet pump 9, first booster pump 1 communicates with second booster pump 2, second booster pump 2 communicates directly with first condenser 3, first condenser 3 is communicated with one port of the second condenser 4 through the first jet pump 6, the first condenser 3 is communicated with the other port of the second condenser 4 through the first auxiliary jet pump 8, and the second condenser 4 is communicated through the second jet pump 7 communicates with one port of the third condenser 5, and the second condenser 4 communicates with the other port of the third condenser 5 through the second auxiliary jet pump. The nozzles 13 of the second booster pump 2 , the first jet pump 6 and th...
Embodiment 2
[0024] image 3 , 4 An embodiment of a five-stage vacuum pump is given. The structure of this embodiment is basically the same as that of Embodiment 1. The difference is that there are three-stage booster pumps. The three-stage booster pumps are connected in sequence. The third booster pump 17 is directly connected to the first condenser 3. connected. All or part of the first jet pump 6 and the first auxiliary jet pump 8 , and the third booster pump 17 are equipped with a vacuum degree throttling adjustment device 10 .
[0025] When in use, it is also divided into two steps of rough vacuum treatment and deep vacuum treatment.
[0026] According to the needs of the actual situation, the vacuum pump system with different stages only needs to add or reduce the number of vacuum pumps, and install all or part of the booster pump, jet pump and auxiliary jet pump directly connected with the first condenser 3 Vacuum degree air-saving adjustment device 10.
PUM
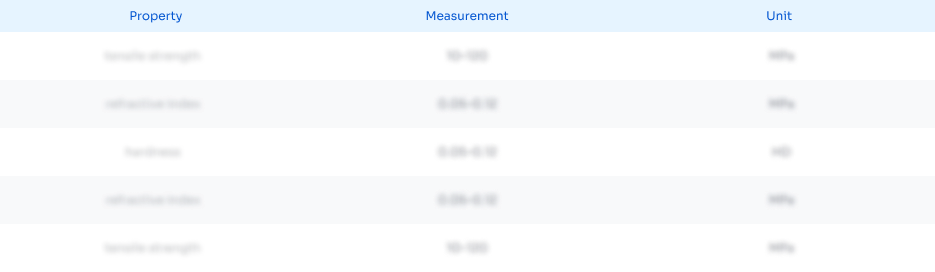
Abstract
Description
Claims
Application Information

- R&D
- Intellectual Property
- Life Sciences
- Materials
- Tech Scout
- Unparalleled Data Quality
- Higher Quality Content
- 60% Fewer Hallucinations
Browse by: Latest US Patents, China's latest patents, Technical Efficacy Thesaurus, Application Domain, Technology Topic, Popular Technical Reports.
© 2025 PatSnap. All rights reserved.Legal|Privacy policy|Modern Slavery Act Transparency Statement|Sitemap|About US| Contact US: help@patsnap.com