Method for purifying polysilicon by adopting electron beam to carry out fractionated smelting
An electron beam melting furnace, polysilicon technology, applied in chemical instruments and methods, silicon compounds, sustainable manufacturing/processing, etc., can solve the problems of hindering the volatilization of phosphorus impurities, removing unfavorable impurities, and large silicon evaporation, and reducing evaporation. Loss, reduce removal efficiency, good purification effect
- Summary
- Abstract
- Description
- Claims
- Application Information
AI Technical Summary
Problems solved by technology
Method used
Image
Examples
Embodiment 1
[0013] The first step of material preparation: Take 500g of polysilicon material with a phosphorus content of 0.001%, wash it with deionized water for 4 times, put it in a drying box and dry it at 50°C, put the polysilicon material into an electron beam melting furnace for melting in the crucible;
[0014] The second step of pretreatment: Use a vacuum pump to vacuum the electron beam melting furnace to below 0.0018Pa; water-cool the melting crucible with cooling at the bottom, and keep the temperature at 40°C; preheat the electron gun, set the high voltage to 30kV, and preheat the high pressure for 5 After 10 minutes, turn off the high voltage, set the beam current of the electron gun to 100mA, and perform preheating. After 15 minutes of preheating, turn off the beam current of the electron gun;
[0015] The third step of purification: turn on the high voltage and beam current of the electron gun, and after stabilization, use the electron gun to bombard the polysilicon materia...
Embodiment 2
[0017] The first step of material preparation: Take 500g of polysilicon material with a phosphorus content of 0.0013%, wash it with deionized water for 4 times, put it in a drying box and dry it at 50°C, put the polysilicon material into an electron beam melting furnace for melting in the crucible;
[0018] The second step of pretreatment: Use a vacuum pump to vacuum the electron beam melting furnace to below 0.0018Pa; water-cool the melting crucible with cooling at the bottom, and keep the temperature at 40°C; preheat the electron gun, set the high voltage to 30kV, and preheat the high pressure for 5 After 10 minutes, turn off the high voltage, set the beam current of the electron gun to 200mA, and perform preheating. After preheating for 10 minutes, turn off the beam current of the electron gun;
[0019] The third step of purification: turn on the high voltage and beam current of the electron gun, and after stabilization, use the electron gun to bombard the polysilicon mater...
Embodiment 3
[0021] The first step of preparing materials is the same as in Example 1;
[0022] The second step of pretreatment: Use a vacuum pump to vacuum the electron beam melting furnace to below 0.0018Pa; water-cool the melting crucible with cooling at the bottom, and keep the temperature at 40°C; preheat the electron gun, set the high voltage to 28kV, and preheat the high pressure for 10 After 10 minutes, turn off the high voltage, set the electron gun beam current to 150mA, and perform preheating. After 15 minutes of preheating, turn off the electron gun beam current;
[0023] The third step of purification: turn on the high voltage and beam current of the electron gun, and after stabilization, use the electron gun to bombard the polysilicon material with high phosphorus content with a beam current of 300mA. Adjust the beam current to 260mA for melting, melt for 8 minutes after melting, reduce the beam current to 0mA again, repeat the operation of 300mA beam current electron beam me...
PUM
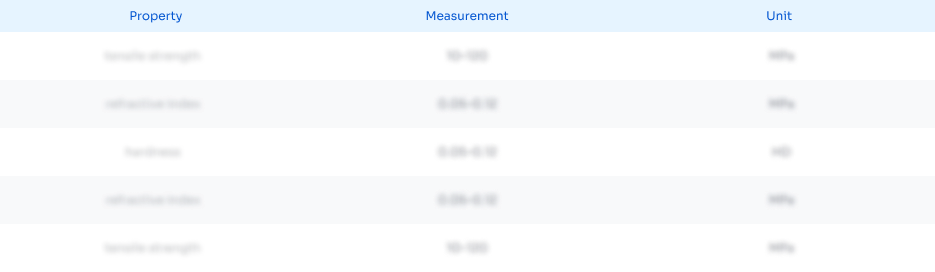
Abstract
Description
Claims
Application Information

- Generate Ideas
- Intellectual Property
- Life Sciences
- Materials
- Tech Scout
- Unparalleled Data Quality
- Higher Quality Content
- 60% Fewer Hallucinations
Browse by: Latest US Patents, China's latest patents, Technical Efficacy Thesaurus, Application Domain, Technology Topic, Popular Technical Reports.
© 2025 PatSnap. All rights reserved.Legal|Privacy policy|Modern Slavery Act Transparency Statement|Sitemap|About US| Contact US: help@patsnap.com