PCB board with heat radiation structure and processing method thereof
A technology of PCB board and heat dissipation structure, which is applied to circuit thermal devices, cooling/ventilation/heating transformation, porous dielectrics, etc. Low, lower thermal resistance effect
- Summary
- Abstract
- Description
- Claims
- Application Information
AI Technical Summary
Problems solved by technology
Method used
Image
Examples
Embodiment Construction
[0027] The general idea of the technical solution of the present invention is: the carrier layer of the PCB board is made into a porous heat-conducting layer with insulation and heat conduction or electrical conduction and heat conduction, and the holes of the porous heat-conducting layer are filled with heat-conducting liquids such as heat-conducting inks or solid-liquid phase change heat-conducting materials, In order to reduce the thermal resistance between the contact interface of the LED and the PCB board, and improve the heat conduction effect of the PCB board.
[0028] The technical solution for realizing the purpose of the invention will be described in detail below in conjunction with the accompanying drawings and embodiments. It should be understood that the specific embodiments described here are only used to explain the present invention, not to limit the present invention.
[0029] Please refer to figure 1 The PCB board with heat dissipation structure proposed ...
PUM
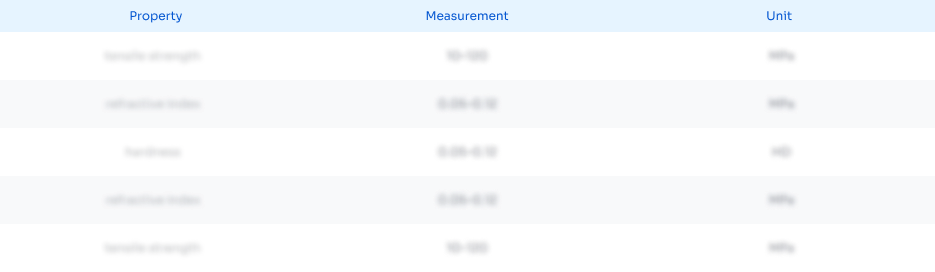
Abstract
Description
Claims
Application Information

- R&D
- Intellectual Property
- Life Sciences
- Materials
- Tech Scout
- Unparalleled Data Quality
- Higher Quality Content
- 60% Fewer Hallucinations
Browse by: Latest US Patents, China's latest patents, Technical Efficacy Thesaurus, Application Domain, Technology Topic, Popular Technical Reports.
© 2025 PatSnap. All rights reserved.Legal|Privacy policy|Modern Slavery Act Transparency Statement|Sitemap|About US| Contact US: help@patsnap.com