Stepped furnace
A ladder furnace and ladder technology, which is applied in furnaces, vertical furnaces, furnace types, etc., can solve problems such as difficulty in practical implementation, and no electric heating and hybrid heating are involved.
- Summary
- Abstract
- Description
- Claims
- Application Information
AI Technical Summary
Problems solved by technology
Method used
Image
Examples
Embodiment 1
[0040] Embodiment one: lightly burned magnesia, calcium oxide, dolomite etc.
[0041] The magnesite, limestone, dolomite, and brucite mined from the mine are washed and calcined in a kiln to 900-1000°C. After a certain period of calcination, the ore is decomposed to produce carbon dioxide gas, and the light calcined product with high activity is obtained. Magnesium oxide, lime and dolomite are important auxiliary materials for building materials, metallurgy and chemical industry. In actual processing, ore lumps should be crushed to below the actual required particle size range, and then crushed without calcination. If fine particles are actually required, the ore should be crushed directly into fine particles, so that the operation in the stepped furnace will be more stable. .
[0042] To calcinate these raw materials in a stepped furnace, first purchase enough light sintered materials (M 1 ) is added to the upper silo (1) with one of the aforementioned various transportatio...
Embodiment 2
[0047] Embodiment 2: sintered alumina, magnesia, mullite, spinel, tabular alumina, magnesia dolomite, etc.
[0048] These clinkers are important refractory raw materials. With the progress of the refractory industry and the change of resources, the firing of clinker has gradually changed from the original natural block material into the furnace for calcination to the crushing of ore into fine powder and calcination of the ball into the furnace. , this method is also the shape of the burden that the ladder furnace operates stably and is easy to control. Of course, the process of pressing balls is mainly for various synthesis and homogenization purposes, and also to improve the grade of clinker and the utilization rate of resources. For step furnace sintering, it is necessary to properly add binder to the pressure balls to increase the strength of the balls, because in the step furnace, the pressure balls are constantly rolling and freely falling downward, and the collision betw...
Embodiment 3
[0053] Embodiment three: sintered cement clinker, alumina clinker
[0054] Cement clinker and alumina clinker are in great demand in the national economy, and my country has become a major producer of cement and alumina. Due to the poor quality of clinker fired in traditional vertical kilns, the country has not allowed vertical kilns to produce cement clinker. However, the economic and cost advantages of shaft kilns still exist, and people have not given up the exploration of shaft kilns that can produce high-quality clinker, and the ladder furnace should be one of them.
[0055] In the rotary kiln, the cement material (pellet material or pre-decomposed powder aggregate particles) is piled up along one side of the wall of the rotary drum, and when it reaches a certain height, it rolls down due to the action of gravity, so that the material continues to rise on the material slope. Roll back and forth, and due to the inclination of the drum, it will advance a certain distance i...
PUM
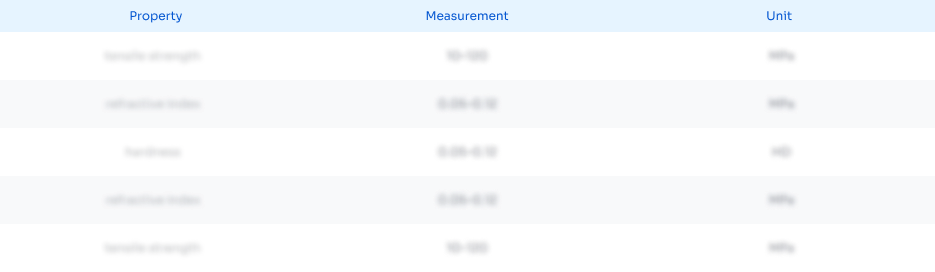
Abstract
Description
Claims
Application Information

- R&D
- Intellectual Property
- Life Sciences
- Materials
- Tech Scout
- Unparalleled Data Quality
- Higher Quality Content
- 60% Fewer Hallucinations
Browse by: Latest US Patents, China's latest patents, Technical Efficacy Thesaurus, Application Domain, Technology Topic, Popular Technical Reports.
© 2025 PatSnap. All rights reserved.Legal|Privacy policy|Modern Slavery Act Transparency Statement|Sitemap|About US| Contact US: help@patsnap.com