Special firebrick for roaster flame path wall and preparation method thereof
A flue wall and refractory brick technology, applied in the field of refractory bricks, can solve the problems of increased heat loss, damage, air leakage and material leakage, etc., and achieve good seismic performance and toughness, stable linear change, and low creep.
- Summary
- Abstract
- Description
- Claims
- Application Information
AI Technical Summary
Problems solved by technology
Method used
Image
Examples
Embodiment 1-1
[0019] Example 1-1: The weight percent content of various components is Al 2 o 3 42. Fe 2 o 3 1.2, CaO+MgO0.7, Na 2 O+K 2 O 0.8, ZrO 2 15. SiC+SiO2 2 10.
Embodiment 1-2
[0020] Embodiment 1-2: the weight percent content of various components is Al 2 o 3 85. Fe 2 o 3 1.5, CaO+MgO0.1, Na 2 O+K 2 O 0.1, ZrO 2 10. SiC+SiO2 2 1.
Embodiment 1-3
[0021] Embodiment 1-3: the weight percent content of various components is Al 2 o 3 50. Fe 2 o 3 1.3, CaO+MgO0.5, Na 2 O+K 2 O 0.4, ZrO 2 12. SiC+SiO2 2 6.
PUM
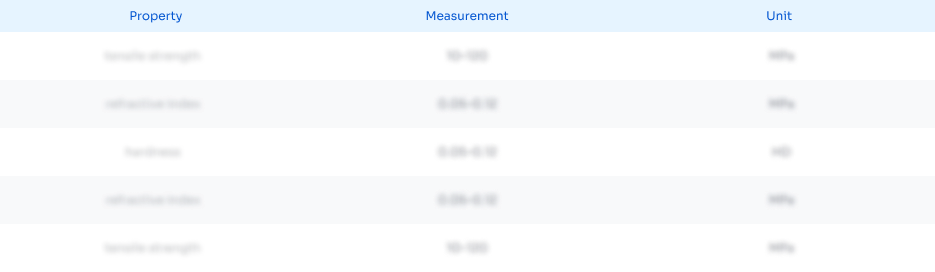
Abstract
Description
Claims
Application Information

- Generate Ideas
- Intellectual Property
- Life Sciences
- Materials
- Tech Scout
- Unparalleled Data Quality
- Higher Quality Content
- 60% Fewer Hallucinations
Browse by: Latest US Patents, China's latest patents, Technical Efficacy Thesaurus, Application Domain, Technology Topic, Popular Technical Reports.
© 2025 PatSnap. All rights reserved.Legal|Privacy policy|Modern Slavery Act Transparency Statement|Sitemap|About US| Contact US: help@patsnap.com