Preparation method of ferric oxide and zinc oxide nanometer composite material
A technology of zinc oxide nano and composite materials, which is applied in the field of preparation of iron oxide-zinc oxide nano composite materials, can solve the problems of long reaction time, serious powder aggregation, poor dispersion, etc., and achieve the goal of shortening the time and improving the photocatalytic performance Effect
- Summary
- Abstract
- Description
- Claims
- Application Information
AI Technical Summary
Problems solved by technology
Method used
Image
Examples
Embodiment 1
[0016] Example 1: 4mmol of nano iron oxide and 1mmol of zinc nitrate were ultrasonically dispersed in 30ml of deionized water, and then 7.5mmol of sodium hydroxide was added, fully stirred and mixed evenly. Add the above solution into a 100ml polytetrafluoroethylene container, tighten the reaction container, put it into a microwave reactor, heat it to 160°C at a heating rate of 18°C / min, and keep it warm for 1h; after cooling down to room temperature, put Pour out the solution in the reaction vessel, then repeatedly wash and filter with deionized water and absolute ethanol until the pH value of the filtered deionized water is neutral; place the obtained red precipitate in an oven at 80°C for 12 hours .
Embodiment 2
[0017] Example 2: 3mmol of nano iron oxide and 1mmol of zinc nitrate were ultrasonically dispersed in 40ml of deionized water, and then 4mmol of sodium hydroxide was added, fully stirred and mixed evenly. Add the above solution into a 100ml polytetrafluoroethylene container, tighten the reaction container, put it into a microwave reactor, heat it to 165°C at a heating rate of 19°C / min, and keep it warm for 0.5h; after cooling down to room temperature, Pour out the solution in the reaction vessel, and then repeatedly wash and filter with deionized water and absolute ethanol until the pH value of the filtered deionized water is neutral; place the obtained red precipitate in an oven at 90°C to dry 11h.
Embodiment 3
[0018] Example 3: 3mmol of nano iron oxide and 1.5mmol of zinc nitrate were ultrasonically dispersed in 40ml of deionized water, and then 7.5mmol of sodium hydroxide was added, fully stirred and mixed evenly. Add the above solution into a 100ml polytetrafluoroethylene container, tighten the reaction container, put it into a microwave reactor, heat it to 170°C at a heating rate of 20°C / min, and keep it warm for 0.3h; after cooling down to room temperature, Pour out the solution in the reaction vessel, and then repeatedly wash and filter with deionized water and absolute ethanol until the pH value of the filtered deionized water is neutral; place the obtained red precipitate in an oven at 95°C to dry 10.5h.
[0019] From figure 1 It can be seen that the iron oxide-zinc oxide composite material prepared in this embodiment is an iron oxide-zinc oxide composite material; figure 2 It can be seen from the figure that in the iron oxide-zinc oxide composite material prepared in this...
PUM
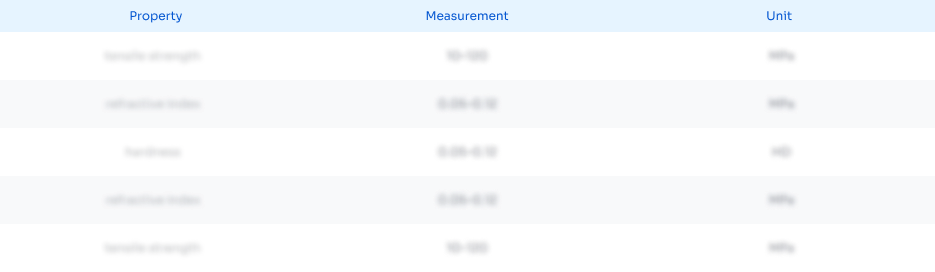
Abstract
Description
Claims
Application Information

- Generate Ideas
- Intellectual Property
- Life Sciences
- Materials
- Tech Scout
- Unparalleled Data Quality
- Higher Quality Content
- 60% Fewer Hallucinations
Browse by: Latest US Patents, China's latest patents, Technical Efficacy Thesaurus, Application Domain, Technology Topic, Popular Technical Reports.
© 2025 PatSnap. All rights reserved.Legal|Privacy policy|Modern Slavery Act Transparency Statement|Sitemap|About US| Contact US: help@patsnap.com