High-conductivity polymer carbon nanotube composite material and micro-processing method thereof
A carbon nanotube, composite material technology, applied in liquid crystal materials, chemical instruments and methods, medical science, etc., can solve the problems of high shear rate, fast injection molding or extrusion rate, uneven distribution of conductivity of polymer materials, etc. , to achieve the effect of simple process and convenient operation
- Summary
- Abstract
- Description
- Claims
- Application Information
AI Technical Summary
Problems solved by technology
Method used
Image
Examples
Embodiment 1
[0038] Extrude 270g of polyurethane pellets and 30g of multi-wall carbon nanotubes with an average diameter of 15nm and a length of about 800nm-5μm through a twin-screw extruder to pelletize once, and control the three-stage processing temperature to 185°C, 195°C , 195°C, rotation speed 120rpm, after processing, carbon nanotubes and polymers form tightly combined pellets. After vacuum drying at a temperature of 100°C, 200g of this pellet and 200g of polyurethane pellets are extruded again through a twin-screw extruder Granulate once, control the three-stage processing temperature at 185°C, 195°C, 195°C, and rotate at 120rpm. The second twin-screw extruded pellets are placed at room temperature for 3 days and then vacuum-dried at 100°C to remove moisture for micro Injection molding, micro-injection plasticizing temperature is 210°C, micro-injection pressure is 77Mpa, injection time is 10s, holding pressure is 20Mpa, and holding time is 10s. After obtaining micro-injection produc...
Embodiment 2
[0040] Extrude 270g of polyethylene pellets, 15g of multi-walled carbon nanotubes with an average diameter of 20nm and a length of about 800nm-5μm, 5g of p-phenylenediamine, and 10g of hexadecyltrimethylammonium bromide through twin-screw extrusion The extruder was extruded and granulated once, and the three-stage processing temperatures of the twin-screw extruder were 185°C, 195°C, and 195°C, respectively, and the rotation speed was 120rpm. After processing, the carbon nanotubes and the polymer formed tightly combined pellets. Place the pellets at room temperature for 3 days, then vacuum-dry them at 100°C to remove moisture for micro-injection molding. The time is 10s, the temperature of the ceramic mold is 25°C, the micro-injection samples are placed at room temperature for 3 days and then annealed at 180°C for 1.5h, and the electrical conductivity is 30S.m -1 .
Embodiment 3
[0042] 27g of polypropylene pellets, 1.5g of multi-walled carbon nanotubes with an average diameter of 20nm and a length of about 800nm-5μm, 0.8g of 2,6-tertiary butyl-4-methylphenol, and ethylene-acrylic acid copolymer 0.7g, extrude and granulate twice through a micro extruder, the micro extrusion temperature is 195°C, the screw speed is 120rpm during the first extrusion, and the residence time is 1min, the screw speed is 500rpm during the second extrusion, and the residence time For 5s, the pellets with carbon nanotubes and polymer tightly combined were obtained. Place the pellets at room temperature for 3 days and then vacuum-dry them at 100°C for micro-injection molding. The micro-injection temperature is 200°C, the micro-injection pressure is 77MPa, the injection time is 10s, the holding pressure is 20Mpa, and the holding time is 50s, the temperature of the ceramic mold is 50°C, the product is placed at room temperature for 3 days and then non-isothermal heat treatment is...
PUM
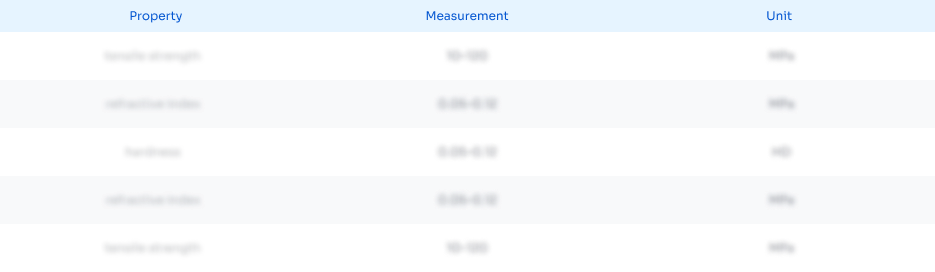
Abstract
Description
Claims
Application Information

- R&D
- Intellectual Property
- Life Sciences
- Materials
- Tech Scout
- Unparalleled Data Quality
- Higher Quality Content
- 60% Fewer Hallucinations
Browse by: Latest US Patents, China's latest patents, Technical Efficacy Thesaurus, Application Domain, Technology Topic, Popular Technical Reports.
© 2025 PatSnap. All rights reserved.Legal|Privacy policy|Modern Slavery Act Transparency Statement|Sitemap|About US| Contact US: help@patsnap.com