Phosphate doped polyaniline anticorrosive paint and preparation method thereof
A technology for anti-corrosion coatings and phosphate esters, applied in anti-corrosion coatings, epoxy resin coatings, coatings, etc., can solve the problems of toxicity and high boiling point, and achieve the effects of easy foaming, low preparation cost and simple synthesis process.
- Summary
- Abstract
- Description
- Claims
- Application Information
AI Technical Summary
Problems solved by technology
Method used
Image
Examples
Embodiment 1
[0042] Embodiment 1: take by weighing 150 grams of epoxy resin E51, 200 grams of dimethylbenzene respectively and put into sand mill tank, under stirring, put into the phosphoric acid ester doped polyaniline powder 10 that is prepared by the phosphoric acid ester of structural formula (1) grams, stirred for 2 hours, under stirring, then added 15 grams of dispersant BYK163, 150 grams of aluminum dihydrogen tripolyphosphate, 150 grams of zinc phosphate, 70 grams of micaceous iron oxide, 60 grams of talcum powder, 50 grams of zinc oxide, precipitated sulfuric acid 40 grams of barium, 5 grams of leveling agent BYK371, stirred for 1 hour at a speed of 2500 rpm, sanded for 2 hours, and filtered with a 200-mesh filter cloth to obtain component A.
[0043] Component B is: 100 grams of curing agent NX-2040;
[0044] Component A and component B were stirred in a high-speed mixer at 1200 rpm for 5 minutes to obtain a phosphate-doped polyaniline anticorrosion coating.
[0045] Spray it o...
Embodiment 2
[0046] Embodiment 2: take by weighing 120 grams of epoxy resin E44, 220 grams of dimethylbenzene respectively and put into sand mill tank, under stirring, put into the phosphoric acid ester doped polyaniline that is prepared by the phosphoric acid ester of (3) by phosphoric acid ester structural formula 20 grams of powder, stirred for 1 hour, then added 10 grams of dispersant BYK163, 200 grams of aluminum dihydrogen tripolyphosphate, 200 grams of zinc phosphate, 100 grams of mica iron oxide, 30 grams of talcum powder, 20 grams of zinc oxide under stirring, and precipitated 10 grams of barium sulfate, 10 grams of leveling agent BYK371, stirred at a speed of 2500 rpm for 0.5 hours, sanded for 3 hours, and filtered with a 200-mesh filter cloth to obtain component A.
[0047] Component B is: 60 grams of curing agent NX-2041;
[0048] Component A and component B were stirred in a high-speed mixer at 1500 rpm for 3 minutes to obtain a phosphate-doped polyaniline anticorrosion coatin...
Embodiment 3
[0050]Embodiment 3: take by weighing 200 grams of epoxy resin E44, 240 grams of dimethylbenzene respectively and put into sand mill tank, under stirring, put into the phosphate-doped polyaniline that is prepared by the phosphoric acid ester of (2) by phosphoric acid ester structural formula 30 grams of powder, stirred for 0.5 hours, then added 5 grams of dispersant BYK163, 130 grams of aluminum dihydrogen tripolyphosphate, 130 grams of zinc phosphate, 60 grams of mica iron oxide, 20 grams of talcum powder, 20 grams of zinc oxide under stirring, and precipitated 10 grams of barium sulfate, 5 grams of leveling agent BYK371, stirred at a speed of 2500 rpm for 3 hours, sanded for 1 hour, and filtered with a 200-mesh filter cloth to obtain component A.
[0051] Component B is: 150 grams of curing agent ZY-650;
[0052] Component A and component B were stirred in a high-speed mixer at 1300 rpm for 4 minutes to obtain a phosphate-doped polyaniline anticorrosion coating.
[0053] Spr...
PUM
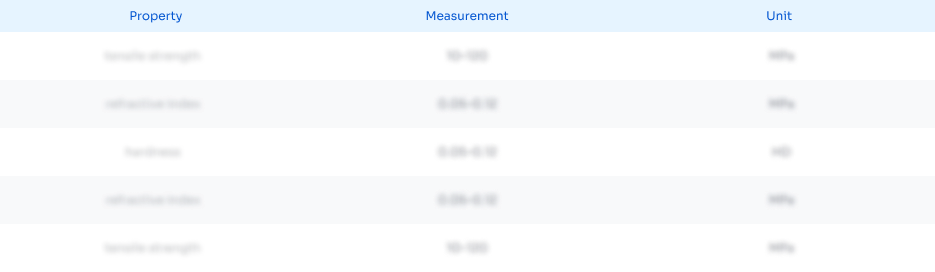
Abstract
Description
Claims
Application Information

- R&D Engineer
- R&D Manager
- IP Professional
- Industry Leading Data Capabilities
- Powerful AI technology
- Patent DNA Extraction
Browse by: Latest US Patents, China's latest patents, Technical Efficacy Thesaurus, Application Domain, Technology Topic, Popular Technical Reports.
© 2024 PatSnap. All rights reserved.Legal|Privacy policy|Modern Slavery Act Transparency Statement|Sitemap|About US| Contact US: help@patsnap.com