Method for comprehensively utilizing chemical byproduct single cryolite
A single cryolite and by-product technology is applied in the field of comprehensive utilization of chemical by-product single cryolite, can solve the problems of no treatment method, environmental pollution, waste of resources, etc., achieves huge environmental protection and social benefits, low price, The effect of high utilization of raw materials
- Summary
- Abstract
- Description
- Claims
- Application Information
AI Technical Summary
Problems solved by technology
Method used
Image
Examples
Embodiment 1
[0020] 1. Using polycrystalline silicon by-product monocryolite and sodium hydroxide solution as raw materials, according to the mass ratio M NaOH :M 单冰晶石 =2.0 React at 60°C for 1 hour to generate hydrogen and sodium aluminate slurry, and recover the hydrogen;
[0021] 2, the mixed slurry prepared in step 1 and hydrofluoric acid are mixed according to the proportion V 混合料浆 :V 氢氟酸 =1︰1 react at 20°C for 1.5h to prepare cryolite slurry;
[0022] 3. Filtrating and washing the cryolite slurry in step 2 to obtain a cryolite ointment for aluminum and a mother liquor, which is used to synthesize other fluoride salts;
[0023] 4. Dry the cryolite ointment for aluminum smelting in step 3 to obtain cryolite for aluminum.
Embodiment 2
[0025] 1. Using polysilicon by-product monocryolite and sodium hydroxide solution as raw materials, according to the mass ratio M NaOH :M 单冰晶石 =3.0 React at 70°C for 3 hours to generate hydrogen and sodium aluminate slurry, and recover the hydrogen;
[0026] 2, the mixed slurry prepared in step 1 and hydrofluoric acid are mixed according to the proportion V 混合料浆 :V 氢氟酸 =2︰1 React at 30°C for 3 hours to prepare cryolite slurry;
[0027] 3. Filtrating, washing and separating the cryolite slurry in step 2 to obtain a cryolite ointment for aluminum and a mother liquor, which is used to synthesize other fluoride salts;
[0028] 4. Dry the aluminum cryolite ointment in step 3 to obtain aluminum cryolite.
Embodiment 3
[0030] 1. Using polysilicon by-product monocryolite and sodium hydroxide solution as raw materials, according to the mass ratio M NaOH :M 单冰晶石 =4.0 React at 100°C for 5 hours to generate hydrogen and sodium aluminate slurry, and recover the hydrogen;
[0031] 2, the mixed slurry prepared in step 1 and hydrofluoric acid are mixed according to the proportion V 混合料浆 :V 氢氟酸 =3︰1 react at 45°C for 4.5h to prepare cryolite slurry;
[0032] 3. Filtrating and washing the cryolite slurry in step 2 to obtain a cryolite ointment for aluminum and a mother liquor, which is used to synthesize other fluoride salts;
[0033] 4. Dry the aluminum cryolite ointment in step 3 to obtain aluminum cryolite.
PUM
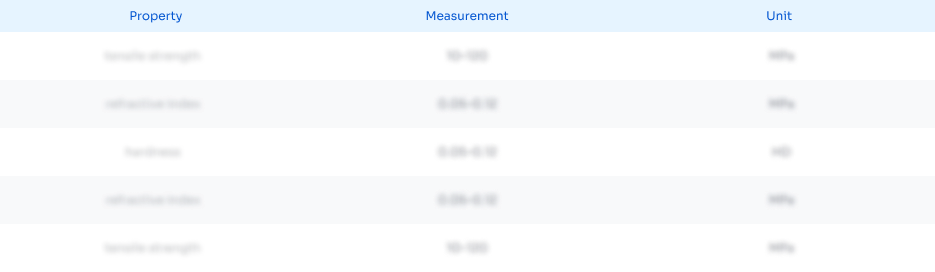
Abstract
Description
Claims
Application Information

- R&D
- Intellectual Property
- Life Sciences
- Materials
- Tech Scout
- Unparalleled Data Quality
- Higher Quality Content
- 60% Fewer Hallucinations
Browse by: Latest US Patents, China's latest patents, Technical Efficacy Thesaurus, Application Domain, Technology Topic, Popular Technical Reports.
© 2025 PatSnap. All rights reserved.Legal|Privacy policy|Modern Slavery Act Transparency Statement|Sitemap|About US| Contact US: help@patsnap.com