Method for producing flame-retardant polyester staple fibers by utilizing recovered polyester bottle chips
A technology of flame retardant polyester and polyester bottle flakes, applied in fiber processing, fire-retardant flame retardant filament manufacturing, single-component polyester rayon, etc. It can solve the problem that the recycled polyester bottle flakes have many impurities and cannot produce high-end chemical fibers. products and other issues, to achieve the effect of being conducive to environmental protection, improving cost performance and reducing production costs
- Summary
- Abstract
- Description
- Claims
- Application Information
AI Technical Summary
Problems solved by technology
Method used
Image
Examples
Embodiment Construction
[0016] A method for producing flame-retardant polyester staple fibers using recycled polyester bottle flakes according to the present invention, see figure 1 , first pretreatment and drying of recycled waste PET bottle flakes. Pretreatment includes a series of raw material preparations such as sorting, crushing, and cleaning the recovered polyester bottle flakes, and then undergoes high-temperature vacuum drying. The drying temperature is 130-160°C, the vacuum degree is 0.06-0.10Mpa, and the drying time is After 8 to 12 hours, the moisture content of the dried bottle flakes is ≤100PPm.
[0017] At the same time, the flame-retardant polyester masterbatch is dried. The flame-retardant polyester masterbatch is put into a large sealed silo, and the dry hot air is introduced into the bottom of the silo. The temperature is kept at 120-140°C, and the drying time is 10-12 hours. , the moisture content of the flame-retardant polyester masterbatch after drying is controlled below 60PPm...
PUM
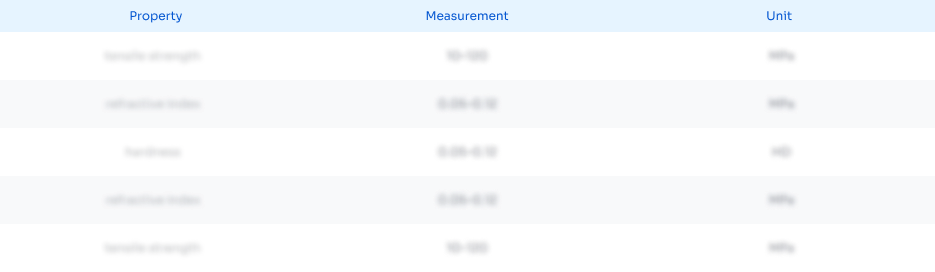
Abstract
Description
Claims
Application Information

- R&D Engineer
- R&D Manager
- IP Professional
- Industry Leading Data Capabilities
- Powerful AI technology
- Patent DNA Extraction
Browse by: Latest US Patents, China's latest patents, Technical Efficacy Thesaurus, Application Domain, Technology Topic, Popular Technical Reports.
© 2024 PatSnap. All rights reserved.Legal|Privacy policy|Modern Slavery Act Transparency Statement|Sitemap|About US| Contact US: help@patsnap.com