Method for continuously preparing polymer and device thereof
A technology for polymers and mixtures, applied in the field of polymer preparation, can solve the problems of high solvent ratio, large heater, poor heating effect, etc., achieve high conversion rate, reduce cost, and achieve the effect of uniform distribution of residence time
- Summary
- Abstract
- Description
- Claims
- Application Information
AI Technical Summary
Problems solved by technology
Method used
Image
Examples
Embodiment 1
[0036] Before carrying out the polymerization reaction, fill each raw material storage tank and reactor with nitrogen (from the nitrogen system) for replacement, remove the oxygen in the raw material liquid and the reactor, and control the oxygen content therein below 2ppm. The composition of the mixed solution was: 61.75 kg methyl methacrylate, 3.25 kg methyl acrylate, 0.20 kg tert-butyl peroxide and 0.33 kg tert-dodecyl mercaptan. According to the formula requirements, the refined and purified methyl methacrylate and methyl acrylate, the free radical initiator di-tert-butyl peroxide and the chain transfer agent tert-dodecyl mercaptan, etc. are fed from the main raw material storage tank 1, The comonomer storage tank 2 and the solvent and / or additive storage tank 3 are transported to the fully mixed reactor 7 through the metering pumps 4, 5 and 6 located at the respective bottoms, respectively. The polymer material is fully mixed in the reactor by ribbon stirring 11, and the ...
Embodiment 2
[0039] Using the same method as in Example 1, the composition of the raw material solution: 61.75kg methyl methacrylate, 1.95kg methyl acrylate, 1.30kg styrene, 0.23kg tert-butyl peroxide and 0.26kg tert-dodecyl sulfide Alcohol (equivalent to the total amount of polymerized monomers). The polymerization temperature in the fully mixed reactor was 140°C. Until the conversion rate reaches 46.0%, the polymerization mixture is transported to the tower reactor connected in series through the gear pump. In the tower reactor, the temperature of the lower tube area is 144°C, and the temperature of the upper tube area is 148°C. When the polymerization conversion rate reaches 84.0%, the polymer mixture is transported to the devolatilization preheater by a high-viscosity gear pump for preheating, wherein the temperature is 230° C., and the devolatilized polymer is stretched and granulated. The aggregation conditions and performance test results are listed in Table 1.
Embodiment 3
[0041] Using the same method as in Example 1, the composition of the raw material solution: 59.9kg methyl methacrylate, 1.85kg methyl acrylate, 3.25kg toluene, 0.25kg tert-butyl peroxide and 0.19kg tert-dodecyl mercaptan . The polymerization temperature in the fully mixed reactor was 135°C. When the conversion rate reaches 50.9%, the polymerization mixture is transported to the tower reactor connected in series through the gear pump. In the tower reactor, the temperature of the lower tube area is 139°C, and the temperature of the upper tube area is 145°C. When the polymerization conversion rate reaches 82.3%, the polymer mixture is transported to the devolatilization preheater for preheating through a high-viscosity gear pump, wherein the temperature is 230° C., and the devolatilized polymer is stretched and granulated. The aggregation conditions and performance test results are listed in Table 1.
PUM
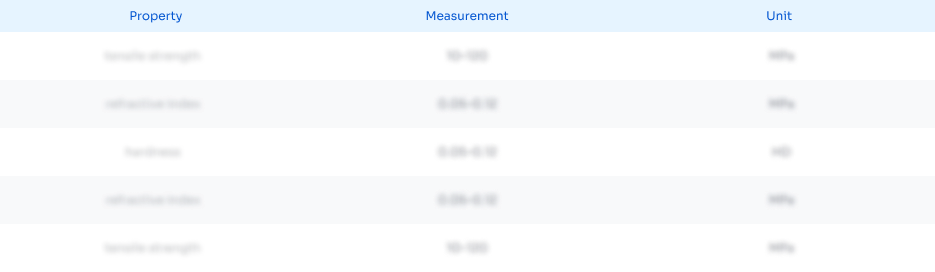
Abstract
Description
Claims
Application Information

- Generate Ideas
- Intellectual Property
- Life Sciences
- Materials
- Tech Scout
- Unparalleled Data Quality
- Higher Quality Content
- 60% Fewer Hallucinations
Browse by: Latest US Patents, China's latest patents, Technical Efficacy Thesaurus, Application Domain, Technology Topic, Popular Technical Reports.
© 2025 PatSnap. All rights reserved.Legal|Privacy policy|Modern Slavery Act Transparency Statement|Sitemap|About US| Contact US: help@patsnap.com