Cutter path generating method for double blade head processing of turbine long blade profile
A tool track and double cutter head technology, applied in the field of mechanical processing, can solve the problems of controlling cutting force, increasing blade processing deformation, and not reflecting double-knife processing, so as to achieve the effect of improving processing efficiency and increasing processing efficiency
- Summary
- Abstract
- Description
- Claims
- Application Information
AI Technical Summary
Problems solved by technology
Method used
Image
Examples
Embodiment Construction
[0045] The present invention is described in further detail below in conjunction with accompanying drawing:
[0046] refer to figure 1 , the working principle of the double-cutter head processing blade is as follows: during processing, the spindle head 1 and the spindle head 2 with the cutter move on both sides of the profile of the blade 3 to be processed. The movement of the two spindle heads is controlled by two separate kinematic mechanisms and coordinated by the overall control system.
[0047] The specific implementation steps of the tool path planning method for double-knife machining are as follows:
[0048] 1) Establish cutting force model
[0049] Firstly, the corresponding mathematical relationship between the cutting force and the inclination angle of the blade machining tool axis is established, and the cutting force model of blade machining is obtained. Since the tool path planning for double-knife machining is based on the cutting force model, it is very impo...
PUM
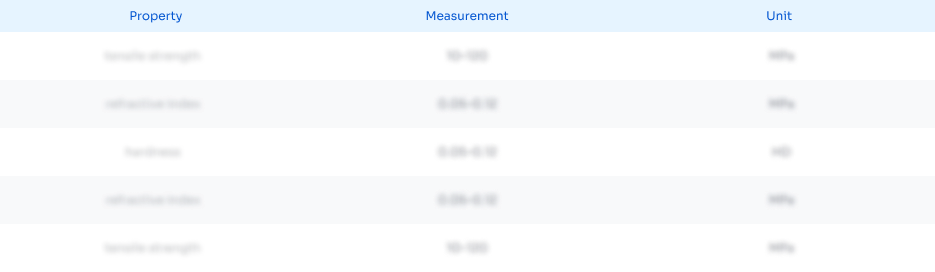
Abstract
Description
Claims
Application Information

- R&D
- Intellectual Property
- Life Sciences
- Materials
- Tech Scout
- Unparalleled Data Quality
- Higher Quality Content
- 60% Fewer Hallucinations
Browse by: Latest US Patents, China's latest patents, Technical Efficacy Thesaurus, Application Domain, Technology Topic, Popular Technical Reports.
© 2025 PatSnap. All rights reserved.Legal|Privacy policy|Modern Slavery Act Transparency Statement|Sitemap|About US| Contact US: help@patsnap.com