Preparation method of molybdenum-cobalt-nickel high-hardness high-strength alloy
A high-strength alloy and high-hardness technology is applied in the field of preparation of molybdenum-cobalt-nickel high-hardness and high-strength alloys, which can solve the problems of reducing wear resistance, cracks, and easy cutting of high-hardness and high-strength alloys.
- Summary
- Abstract
- Description
- Claims
- Application Information
AI Technical Summary
Problems solved by technology
Method used
Image
Examples
Embodiment
[0011] The specific embodiment of the preparation method of the molybdenum-cobalt-nickel high-hardness and high-strength alloy of the present invention comprises first compounding compound carbide, cobalt powder and molybdenum carbide powder into a mixture according to certain requirements, and then unloading after wet grinding in a ball mill for 80 to 83 hours, Re-precipitate for 24 hours, dry and 100-mesh vibrating sieve, mix molding agent, press, release molding agent and keep warm at (1480-1500) ° C for 50 minutes for sintering and other processes.
[0012] Table 1 provides specific examples of the aforementioned chemical composition of the mixture and related batching methods. Table 2 provides the Rockwell hardness and flexural strength values of molybdenum-cobalt-nickel high-hardness and high-strength alloys prepared according to the five specific examples in Table 1.
[0013] Table 1
[0014]
[0015] Table 2
[0016] Numbering
PUM
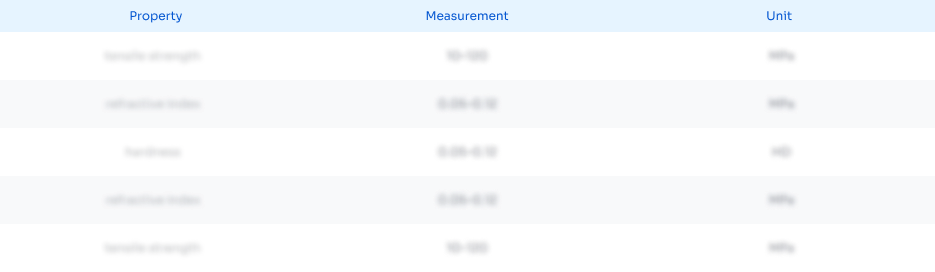
Abstract
Description
Claims
Application Information

- R&D
- Intellectual Property
- Life Sciences
- Materials
- Tech Scout
- Unparalleled Data Quality
- Higher Quality Content
- 60% Fewer Hallucinations
Browse by: Latest US Patents, China's latest patents, Technical Efficacy Thesaurus, Application Domain, Technology Topic, Popular Technical Reports.
© 2025 PatSnap. All rights reserved.Legal|Privacy policy|Modern Slavery Act Transparency Statement|Sitemap|About US| Contact US: help@patsnap.com