Method for preparing high-purity Ti3AlC2 ceramics
A ceramic and high-purity technology, applied in the field of material science, can solve the problems of narrow reaction temperature range, influence on purity, and high preparation temperature, and achieve the effects of convenient operation, increased reactivity and high purity
- Summary
- Abstract
- Description
- Claims
- Application Information
AI Technical Summary
Problems solved by technology
Method used
Image
Examples
Embodiment 1
[0016] 1) First, get TiC powder, Ti powder and Al powder and mix according to the atomic ratio of TiC powder: Ti powder: Al powder=2.0:1.0:1.0;
[0017] 2) Next, put the mixed powder into a stainless steel ball milling tank, add 0.5% of the mass of the mixed powder to sodium stearate as a dispersant, and 50% ethanol as a ball milling aid to make a mixture for ball milling. It is a steel ball, the mill speed is 800 rpm, the mass ratio of the ball to the mixture is 8:1, and the ball mill is milled for 4 hours to obtain a fine powder and dried;
[0018] 3) Then, pre-press the dried mixture into a cake shape, put it into a graphite mold, and raise the temperature from room temperature to 300°C at a rate of 5°C / min under vacuum, and then increase the temperature at a rate of 10°C / min The temperature is raised to 1500°C, and when the temperature reaches 700°C, pressurization is started to make the pressure reach 20MPa, and the temperature is kept for 2 hours;
[0019] 4) Finally, a...
Embodiment 2
[0024] 1) First, get TiC powder, Ti powder and Al powder and mix according to the atomic ratio of TiC powder: Ti powder: Al powder=2.0:1.0:1.0;
[0025] 2) Next, put the mixed powder into a stainless steel ball milling tank, add 0.5% of the mass of the mixed powder to sodium stearate as a dispersant, and 40% ethanol as a ball milling aid to make a mixture for ball milling. It is a steel ball, the mill speed is 800 rpm, the mass ratio of the ball to the mixture is 8:1, and the ball mill is milled for 4 hours to obtain a fine powder and dried;
[0026] 3) Then, pre-press the dried mixture into a cake shape, put it into a graphite mold, and raise the temperature from room temperature to 300°C at a rate of 10°C / min under vacuum, and then increase the temperature at a rate of 20°C / min The temperature is raised to 1450°C, and when the temperature reaches 700°C, pressurization is started to make the pressure reach 20MPa, and the temperature is maintained for 2 hours;
[0027] 4) Fin...
Embodiment 3
[0032] 1) First, get TiC powder, Ti powder and Al powder and mix according to the atomic ratio of TiC powder: Ti powder: Al powder=2.0:1.0:1.2;
[0033] 2) Next, put the mixed powder into a stainless steel ball mill jar, add 1.2% sodium stearate as a dispersant and 60% ethanol as a ball milling aid to make a mixture for ball milling, and the grinding medium It is a steel ball, the mill speed is 1000 rpm, the mass ratio of the ball to the mixture is 12:1, and the ball mills for 2 hours to obtain a fine powder and dry it;
[0034] 3) Then, pre-press the dried mixture into a cake shape, put it into a graphite mold, raise the temperature from room temperature to 1300°C at a rate of 20°C / min under vacuum, and start pressurizing when the temperature reaches 700°C Make the pressure reach 10MPa, keep the heat and pressure for 0.5 hours;
[0035] 4) Finally, after the heat preservation and pressure holding are completed, the Ti 3 AlC 2 ceramics.
PUM
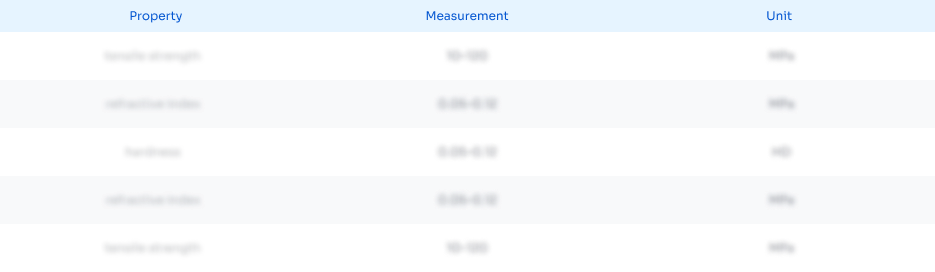
Abstract
Description
Claims
Application Information

- R&D
- Intellectual Property
- Life Sciences
- Materials
- Tech Scout
- Unparalleled Data Quality
- Higher Quality Content
- 60% Fewer Hallucinations
Browse by: Latest US Patents, China's latest patents, Technical Efficacy Thesaurus, Application Domain, Technology Topic, Popular Technical Reports.
© 2025 PatSnap. All rights reserved.Legal|Privacy policy|Modern Slavery Act Transparency Statement|Sitemap|About US| Contact US: help@patsnap.com