Method for hoisting, roasting and casting strip continuous casting flow distribution device
A casting method and flow distributor technology are applied in the field of thin strip continuous casting, which can solve the problems of reducing the molten pool surface temperature, broken belt, overflowing steel or broken belt, etc. The effect of reducing production costs and reducing shrinkage time
- Summary
- Abstract
- Description
- Claims
- Application Information
AI Technical Summary
Problems solved by technology
Method used
Image
Examples
Embodiment 1
[0037] see Figure 1 ~ Figure 3 , which shows the first embodiment of the present invention. The flow distributor 1 is installed at both ends of the bottom of the tundish car 3 through the hanging mechanism 2, the distributor 4 is installed at the bottom of the tundish car 3, the distributor 4 is inserted into the flow distributor 1, and the tundish car 3 carries the flow distributor 1 and distribution The device 4 moves up and down together;
[0038] The hanging mechanism 2 includes a suspension rod 21 and a fixed bracket 22; the upper end of the fixed bracket 22 is fixed at both ends of the bottom of the tundish car 3, and the fixed bracket 22 is provided with an inclined chute 221 that enables the upper end of the suspension rod to move up and down; The flow distributor 1 is set at the lower end of the boom 21; after reaching the casting position, the boom 21 hangs the flow distributor 1 and then descends, and adjusts the upper and lower positions of the tundish car 3, so th...
Embodiment 2
[0045] see Figure 4 ~ Figure 7 , which shows the second embodiment of the present invention. Another structural form of the hanging mechanism 2 according to the present invention includes two fixed frames 24, two pairs of hanging claws 25, two gear sets 26, and a movable slide plate 27; the fixed frames 24 are installed on both sides of the tundish car 3, fixed The frame 24 is provided with a track 241 for lifting the upper end of the hanging claw 25; each pair of hanging claws 25 is cross-connected by a central axis; the gear set 26 is arranged on the fixed frame 24, and the moving slide plate 27 is a T-shaped structure, and the side of the middle boss It is a rack structure, which cooperates with the gear set 26 gears, and the other end is connected to the central shaft 251 between the two pairs of hanging claws 25;
[0046] The tundish car 3 has an independent hydraulic lifting mechanism, which moves up and down together with the hanging mechanism 2 to adjust the up and d...
PUM
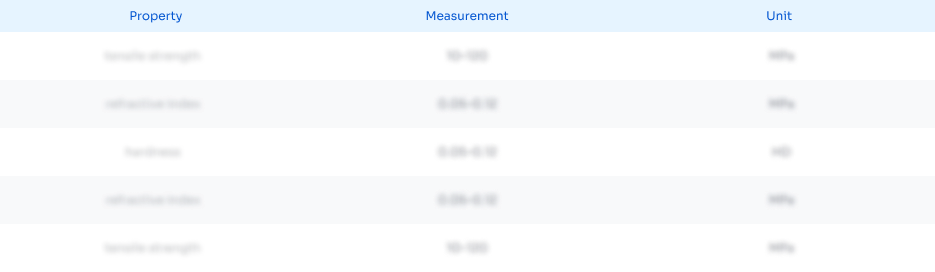
Abstract
Description
Claims
Application Information

- Generate Ideas
- Intellectual Property
- Life Sciences
- Materials
- Tech Scout
- Unparalleled Data Quality
- Higher Quality Content
- 60% Fewer Hallucinations
Browse by: Latest US Patents, China's latest patents, Technical Efficacy Thesaurus, Application Domain, Technology Topic, Popular Technical Reports.
© 2025 PatSnap. All rights reserved.Legal|Privacy policy|Modern Slavery Act Transparency Statement|Sitemap|About US| Contact US: help@patsnap.com