Composite material of skutterudite filling substrate and preparation method thereof
A technology for filling skutterudite and composite materials, which is applied in the direction of cobalt compounds, chemical instruments and methods, and thermoelectric device node lead-out materials, etc. melting point etc.
- Summary
- Abstract
- Description
- Claims
- Application Information
AI Technical Summary
Problems solved by technology
Method used
Image
Examples
preparation example Construction
[0116] The preparation method of composite material of the present invention comprises the steps:
[0117] Weighing and packaging I, Co, Sb and Ga, the weighing process is carried out according to the stoichiometric ratio, wherein I is at least one of Yb, Eu, Ce, La, Nd, Ba and Sr,
[0118] obtaining a molten mixture of I, Co, Sb and Ga, wherein I is at least one of Yb, Eu, Ce, La, Nd, Ba and Sr,
[0119] said molten mixture is quenched to form a solid bulk material;
[0120] The solid matrix material is annealed; the annealed solid matrix material is obtained
[0121] The annealed solid matrix material is made into powder;
[0122] The powder is consolidating to form the composite material.
[0123] Specifically, the melting temperature of the molten mixture is 1000-1200°C.
[0124] Specifically, a quenching medium selected from air, water, brine, oil or liquid nitrogen or other quenching methods are used for quenching. Other quenching methods include Melt spinning and t...
Embodiment 1
[0146] The high-purity metal raw materials Yb block, Co block, Sb block, and Ga block are mixed in the glove box according to the molar ratio of 0.26:4:12:0 and 0.26:4:12.2:0.2, respectively, and the raw materials are sealed in the inner wall for evaporation. The carbon-filmed quartz tube is sealed with an argon plasma flame while drawing a vacuum. The packaged quartz tube was heated to 1100°C at a heating rate of 2°C / min and held for 20 hours, then quenched in saturated brine. The quenched ingot and the quartz tube were annealed at 730°C for 240 hours to obtain the composition Yb 0.26 co 4 Sb 12 and Yb 0.26 co 4 Sb 12 / 1.2mol% GaSb bulk. After the block is ground into fine powder, discharge plasma sintering is carried out, the sintering temperature is 600°C, the holding time is 5 minutes, and the pressure is 50MPa. The phase analysis, microstructure and thermoelectric properties of the obtained materials are as follows: Figure 4-9 shown.
Embodiment 2
[0148] The high-purity raw materials Yb block, Co block, Sb block, and Ga block are mixed in a glove box at a molar ratio of 0.26:4:12.3:0.3, and the raw materials are sealed in a quartz tube with a built-in tantalum foil crucible. Encapsulation was performed with an argon plasma flame. The packaged quartz tube was heated to 1200°C at a heating rate of 3°C / min and held for 10 hours, then quenched in saturated brine. The quenched ingot and the quartz tube were annealed at 750°C for 300 hours to obtain a composition of Yb 0.26 co 4 Sb 12 / 1.8mol% GaSb bulk. After the block is ground into fine powder, discharge plasma sintering is carried out, the sintering temperature is 600°C, the holding time is 10 minutes, and the pressure is 60MPa. The maximum ZT value of the obtained composite thermoelectric material is 1.35 (850K).
PUM
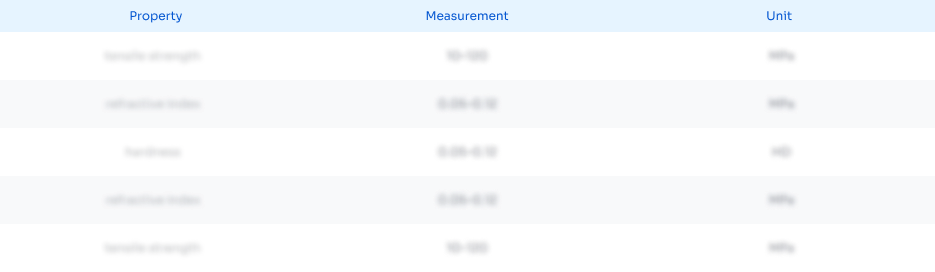
Abstract
Description
Claims
Application Information

- R&D
- Intellectual Property
- Life Sciences
- Materials
- Tech Scout
- Unparalleled Data Quality
- Higher Quality Content
- 60% Fewer Hallucinations
Browse by: Latest US Patents, China's latest patents, Technical Efficacy Thesaurus, Application Domain, Technology Topic, Popular Technical Reports.
© 2025 PatSnap. All rights reserved.Legal|Privacy policy|Modern Slavery Act Transparency Statement|Sitemap|About US| Contact US: help@patsnap.com