Anti-corrosion coating for surface of steel structure and preparation method thereof
An anti-corrosion coating and steel structure technology, applied in anti-corrosion coatings, epoxy resin coatings, coatings, etc., can solve the problems of rough film formation, poor water permeability, and high powder content in the primer, saving man-hours and construction. Effects of cost, high corrosion resistance and adhesion
- Summary
- Abstract
- Description
- Claims
- Application Information
AI Technical Summary
Problems solved by technology
Method used
Examples
Embodiment 1
[0064] Primer preparation
[0065] A component modified epoxy resin 5.0g
[0067] B component water-based epoxy resin curing agent 10.00 g
[0068] Aluminum tripolyphosphate 5.00 g
[0069] Titanium dioxide 1.00g
[0071] Barite 2.00g
[0072] Nano Fumed Silica 0.20g
[0073] Iron Oxide Red 1.00g
[0074] Deionized water 10.00g
[0075] Component C deionized water 1.00g
[0076] Preparation Process
[0077] First the above-mentioned water-based epoxy resin curing agent by weight is diluted with half of the amount of deionized water in the B component by the above-mentioned parts by weight, then stir and add the above-mentioned titanium dioxide by weight, talcum powder, weight Spar, nano meteorological silica, iron oxide red, after stirring at high speed for 5 minutes, then dilute with the remaining deionized...
Embodiment 2
[0116] Primer preparation
[0117] A component modified epoxy resin 5.00g
[0119] B component water-based epoxy resin curing agent 30.00 grams
[0120] Aluminum tripolyphosphate 11.00 g
[0121] Titanium dioxide 1.00g
[0122] Talc powder 10.00 g
[0123] Barite 10.00g
[0124] Nano Fumed Silica 1.50g
[0125] Iron Oxide Red 5.00g
[0126] Deionized water 25.00g
[0127] C component deionized water 20.00g
[0128] Preparation Process
[0129] First the above-mentioned water-based epoxy resin curing agent by weight is diluted with half of the amount of deionized water in the B component by the above-mentioned parts by weight, then stir and add the above-mentioned titanium dioxide by weight, talcum powder, weight Spar, nano meteorological silica, iron oxide red, after stirring at high speed for 10 minutes, then dilute with the remaining deionized water in component B...
Embodiment 3
[0165] Primer preparation
[0166] A component modified epoxy resin 5 grams
[0168] B component water-based epoxy resin curing agent 23.46 grams
[0169] Aluminum tripolyphosphate 5.13g
[0170] Titanium dioxide 2.73 grams
[0171] Talc powder 5.13g
[0172] Barite 5.13g
[0173] Nano Fumed Silica 1.03g
[0174] Iron Oxide Red 2.73g
[0175] Deionized water 22.41g
[0176] Component C deionized water 19.51g
[0177] Preparation Process
[0178] First the above-mentioned water-based epoxy resin curing agent by weight is diluted with half of the amount of deionized water in the B component by the above-mentioned parts by weight, then stir and add the above-mentioned titanium dioxide by weight, talcum powder, weight Spar, nano meteorological silica, iron oxide red, after stirring at high speed for 8 minutes, then dilute with the remaining ...
PUM
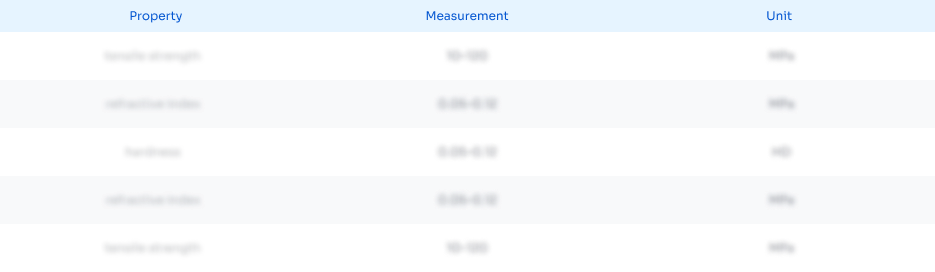
Abstract
Description
Claims
Application Information

- Generate Ideas
- Intellectual Property
- Life Sciences
- Materials
- Tech Scout
- Unparalleled Data Quality
- Higher Quality Content
- 60% Fewer Hallucinations
Browse by: Latest US Patents, China's latest patents, Technical Efficacy Thesaurus, Application Domain, Technology Topic, Popular Technical Reports.
© 2025 PatSnap. All rights reserved.Legal|Privacy policy|Modern Slavery Act Transparency Statement|Sitemap|About US| Contact US: help@patsnap.com